Get down on it!
Presenting a simple, yet revolutionary way to install monopiles, endorsed by industry leaders. Jan van der Tempel, CEO at Delft Offshore Turbine, and Sander Suur, design manager at Van Oord, share their insights on the simplicity and success of the slip joint technology.
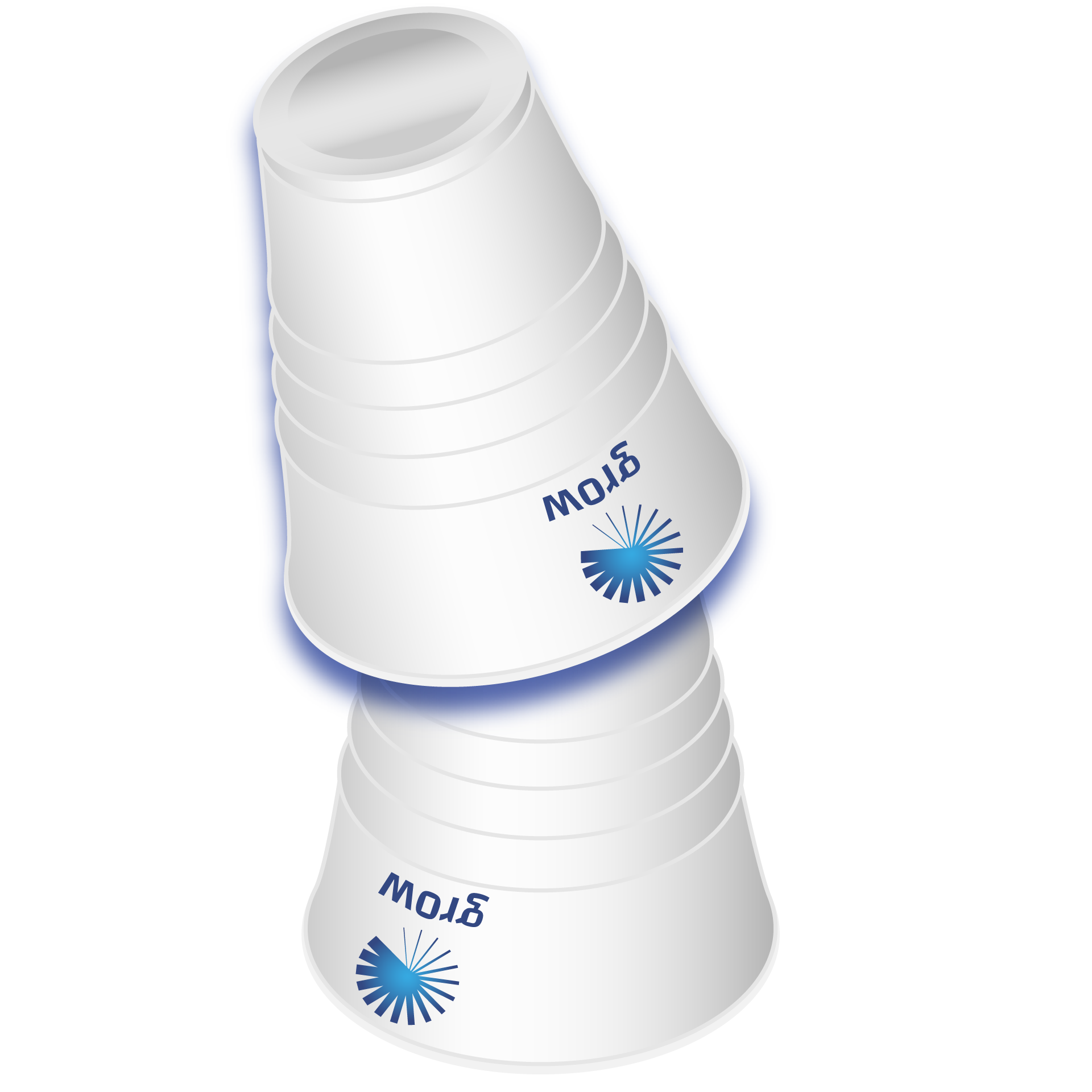
The slip joint
Jan’s first encounter with the slip joint technology was back in 2002, during the early stages of his PhD. “We had a meeting, and one of the turbine guys said, ‘Hey, did you know about a wind turbine with a slip joint?’. We wrote a little report, and we thought, well, this is so simple; let’s go and do it! And 22 years later, here we are.”
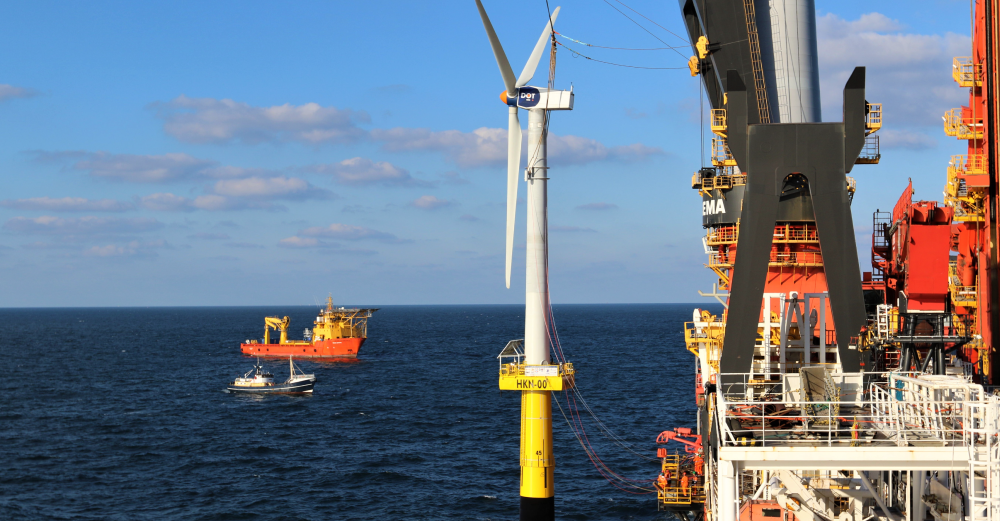
The advantages
Have a look at Sander's profile on LinkedIn
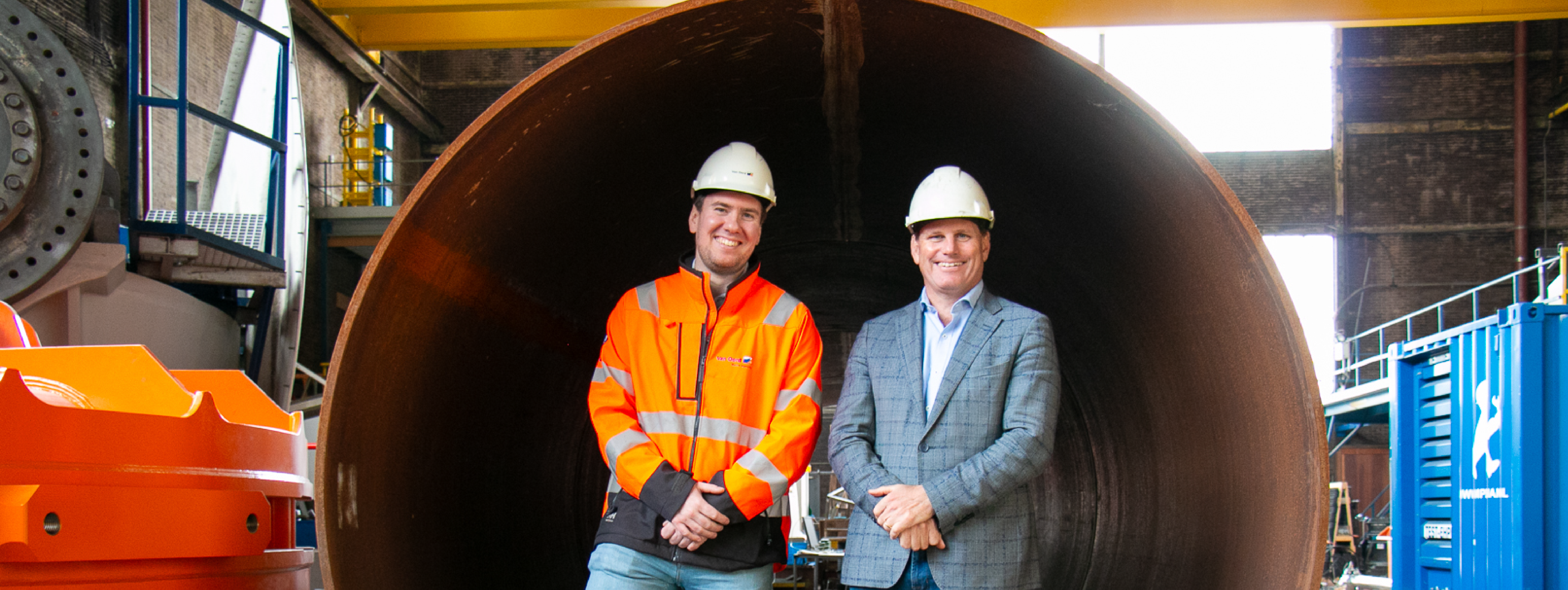
How is it done now
With current methods, the installation takes much longer. With a grouted connection, you always need temporary support. You first sink the structure over the monopile before you pour in the grout. You need additional features to keep the grout in place. After pouring in the concrete, you must wait for it to cure. So you need more vessels and much more time. Because of the risk of instability in the longer term – lessons learned in the early days of offshore wind – grouting is no longer a preferred option.
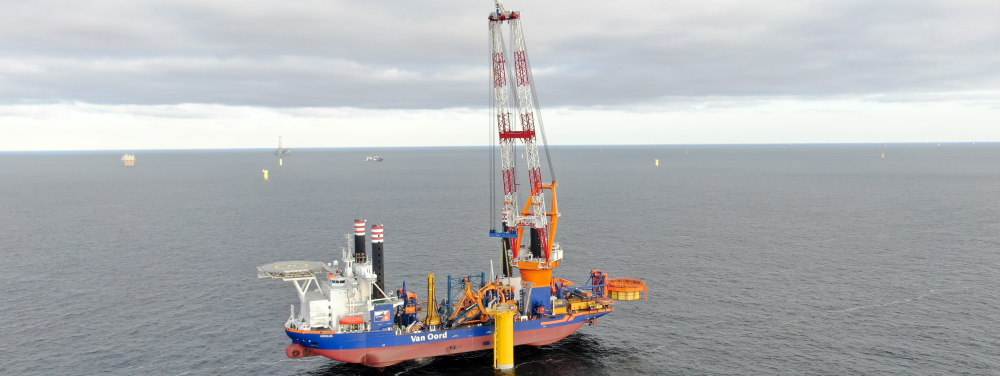
For a bolted connection, you need a monopile with an expensive flange that can not be hammered to keep the flange intact. Then, you have to lift very accurately and position the boltholes so that they are precisely across each other. Then we need to go in and put in and tighten the bolts (approximately 100 to 150 per turbine). These are enormous; they are the size of your upper leg nowadays. During their lifetime, we need to check the operational functionality of the bolts, e.g. every one to two years.
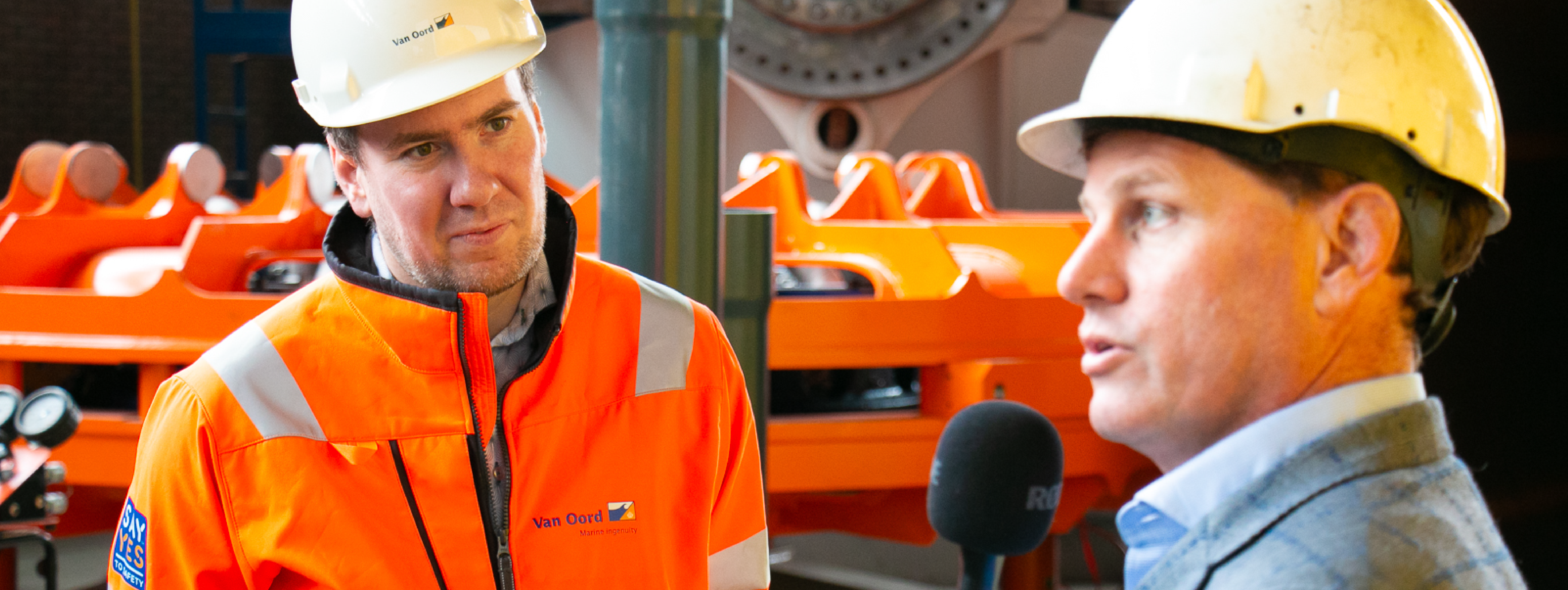
Long way
If the advantages are so clear, why has it taken so long for the technology to become more prominent? Jan grimaces. “We have a very, very strong-headed industry that loves to do financial calculations. Looking at innovation, they challenge that; they challenge us continuously with all sorts of questions. So basically, already for 22 years, we’re putting our money where our mouth is - and we put the steel in the water.”
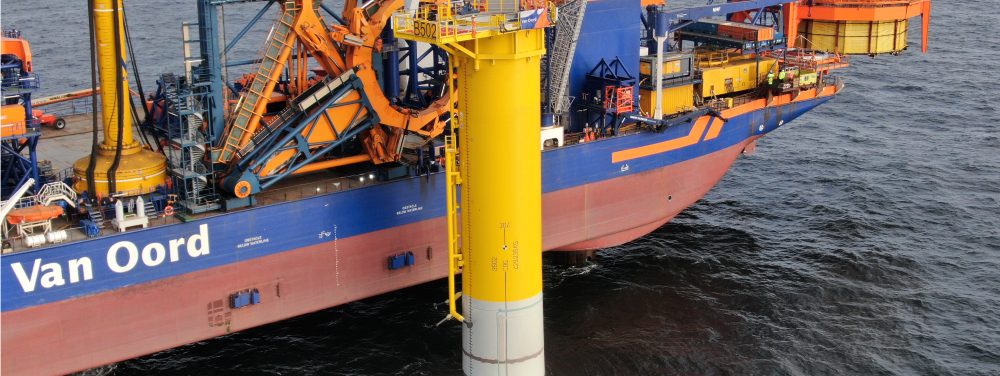
Many projects and tests have been executed with many different partners. First, the slip joint was tested on the Maasvlakte in the Netherlands; then, it was taken offshore and demonstrated for a full year in the SJOR project at the Prinses Amalia Windpark. We gained a lot of knowledge about the installation and removal process and also about the behaviour of the connection itself. The biggest thing we learned was how the pile sinks when you add a coating and that there is an endpoint to the slipping of the joint.
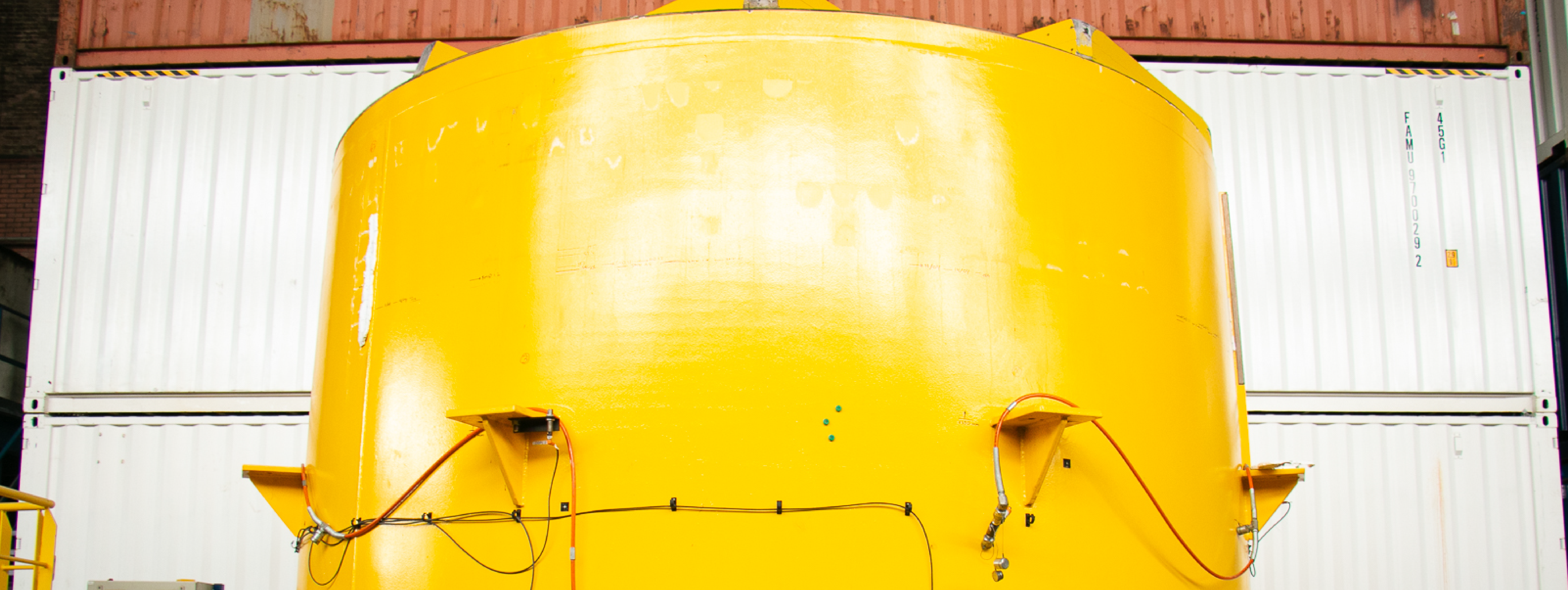
There was also an additional project called SJOQ, where even more measurements were done. All the results were entered into Van Oord's calculation tool. “Together with certifying bodies, we did a lot of work, and then Van Oord took over. In a consortium together with Investri Offshore and Green Giraffe, called Two Towers, Van Oord installed a full-scale slip joint with a 9,5 MW turbine on top of it for the first time in 2020.
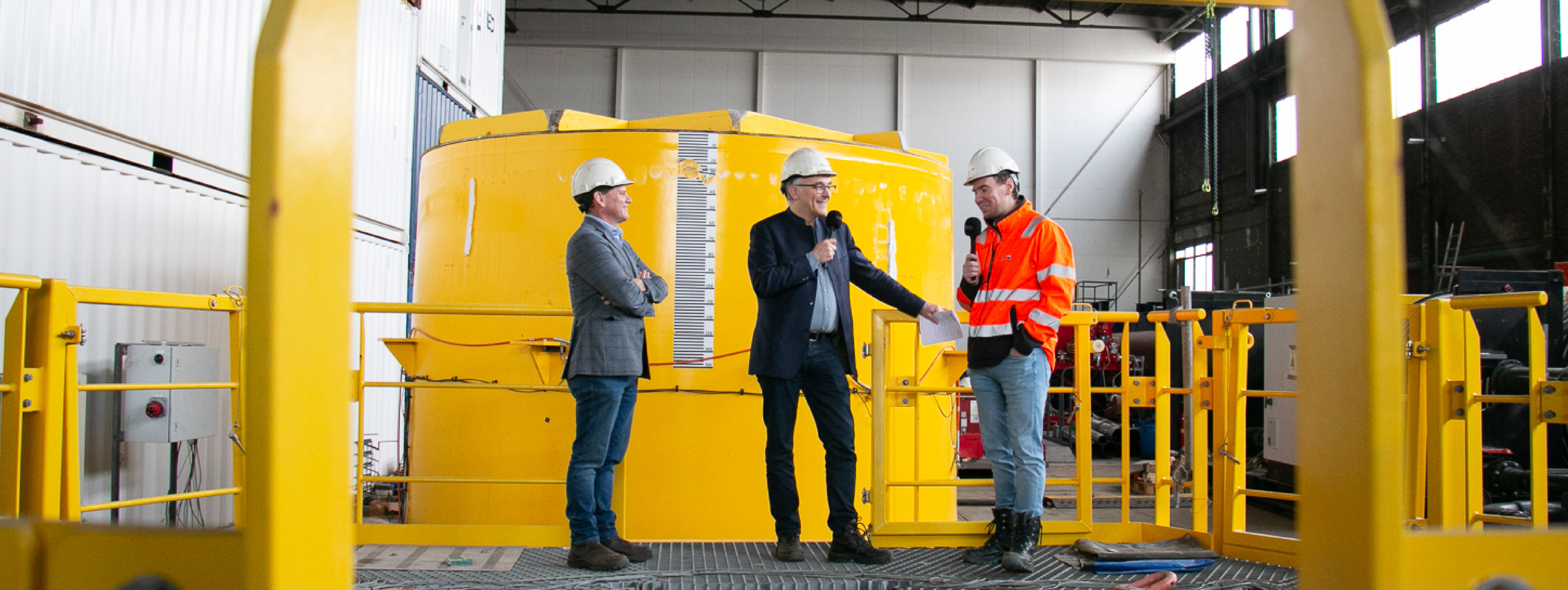
Before installing the Borssele V turbine, Van Oord did additional testing on smaller scales to push the load levels because the turbine in the SJOR and SJOQ projects was relatively small. They wanted to see how the slip joint would behave then. Finally, Van Oord wanted to learn more about corrosion in the slip joint. Tests showed that the technology lasts for the lifetime of a wind farm.
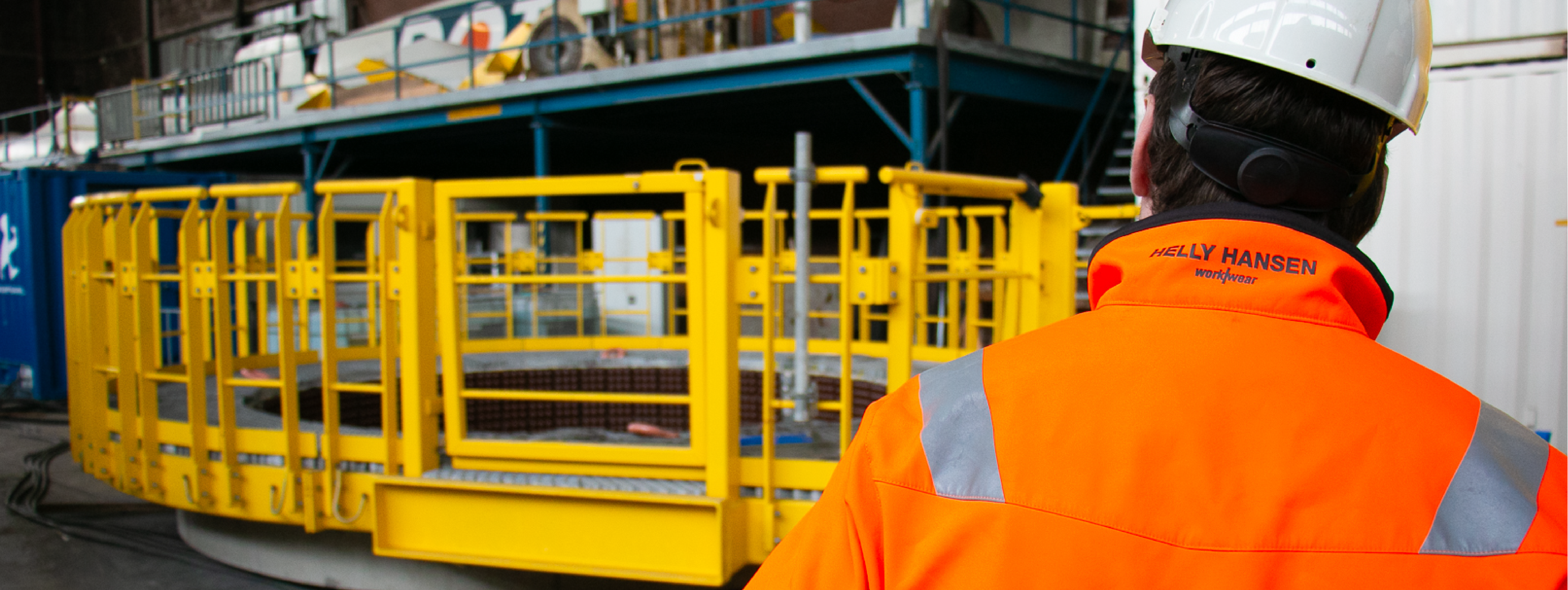
Above and below water
The slip joint connection was initially tested above the water surface. But “we decided to challenge ourselves in Borssele V. We wanted to prove the business case for the slip joint. Putting the slip joint underwater lets you optimise the weight split between the monopile and transition piece. And there is no reason why you should not design an underwater joint. So we wanted to demonstrate to the whole industry that it works and is certifiable.” Sander explains. So now all the checks and balances have been passed, the technology has been certified, and we expect that this technology will be applied for the installation of monopiles in many projects.
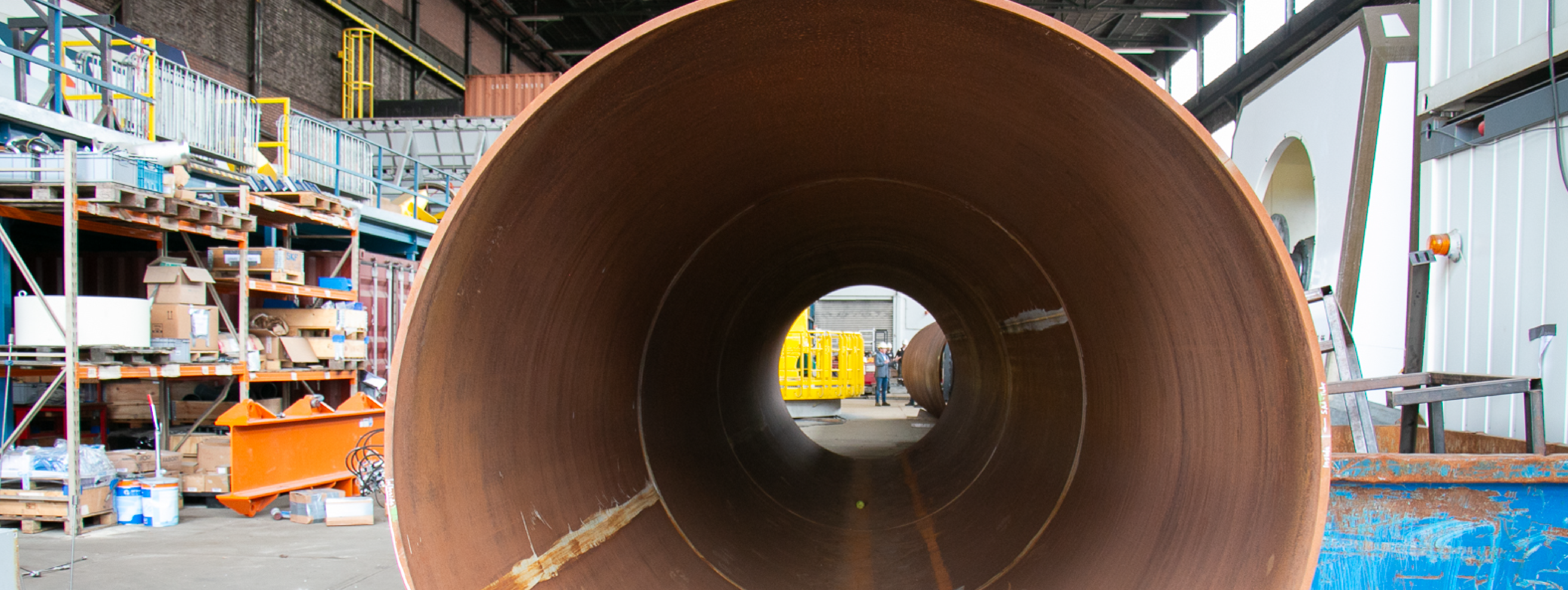
Boring is good
We are still actively monitoring the slip joint in Borssele V, for example, the occurrence of corrosion and the possibility of fatigue. We track the changes. And? “The results are boring.” The fatigue behaviour is exactly as expected, and there’s nothing happening in terms of corrosion.
Find out more about the SJOR project

A spin-off: the Skybox
You can also use the slip joint for other purposes. It is just a smart connection to join two cylinders. So, a spin-off of the project is the Skybox. It is a combination of the steel platform and the slip joint technology. The inside of the main platform is also conical, and you can slide it across anything. They are now testing this concept and measure quite in detail how it works and what’s happening.” Jan says. “It has even already been applied in the offshore FOX project.”
Jan concludes: “So we continue to innovate and improve with what we have learned in the projects. The slip joint is a proven technology, and there is really no reason why you should not build offshore wind farms with slip joints. It is easy, fast, safe, and cost-effective. So we challenge the industry to start applying the slip joint.”
DOT: expertise in new offshore wind energy concepts
Eneco: expertise in project development and operating wind farms
Heerema Marine Contractors: expertise in installation
Sif: expertise in manufacturing of monopiles
TNO: expertise in applied research
TU Delft: expertise in engineering structures
Van Oord: expertise in installation
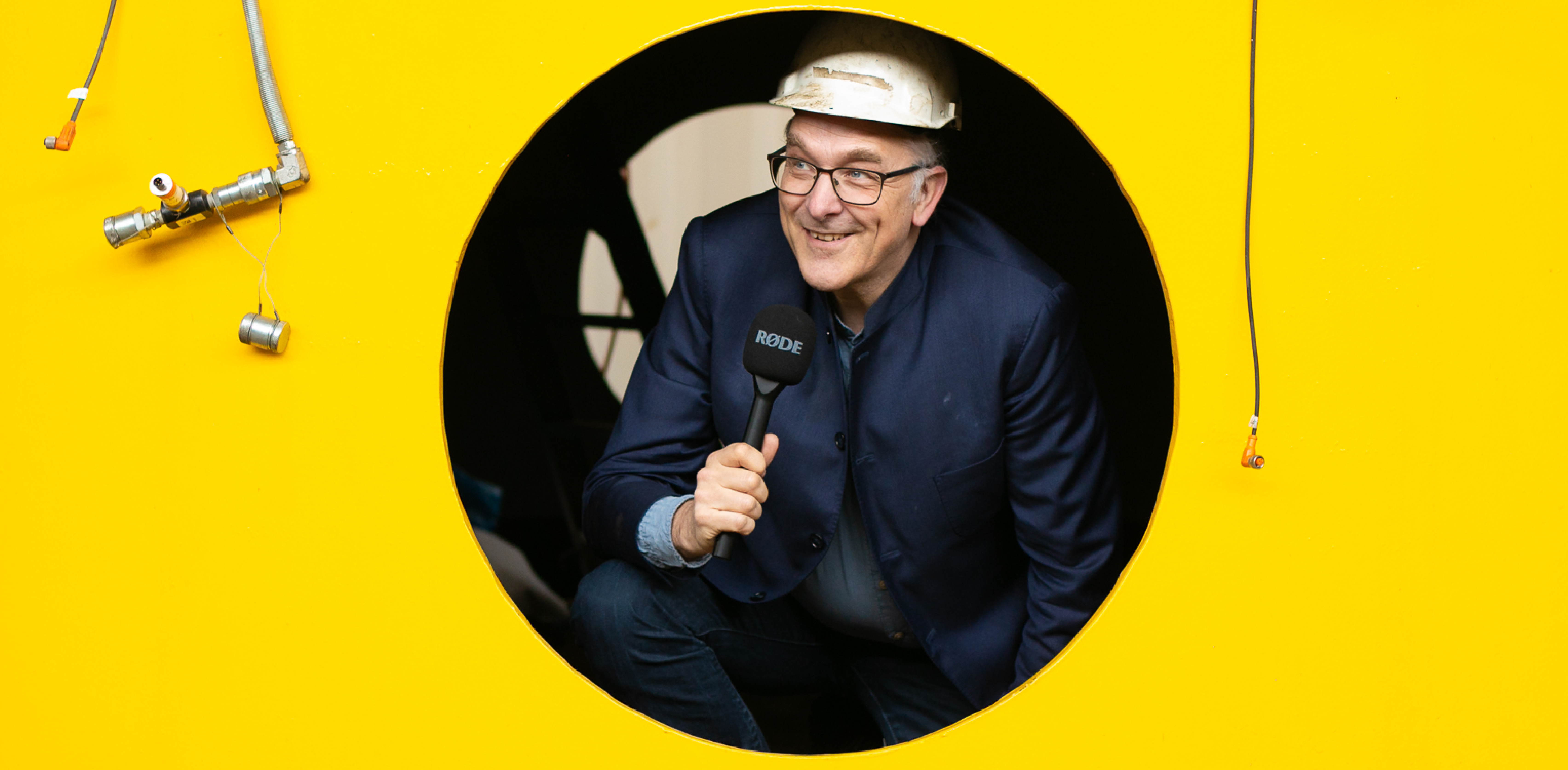
© GROW ’25