The Blade Runner and the Blade Crawler
In the last two decades, the length of the rotor blades for offshore wind turbines has increased significantly. Where we started with blade lengths ranging between 30 and 40 metres, we are now reaching 110-120 metres in length per blade, and this may go up towards an impressive 150 metres in the future. Despite efforts to improve control over the manufacturing process, defects still occur during production and operation that may lead to blade failures.
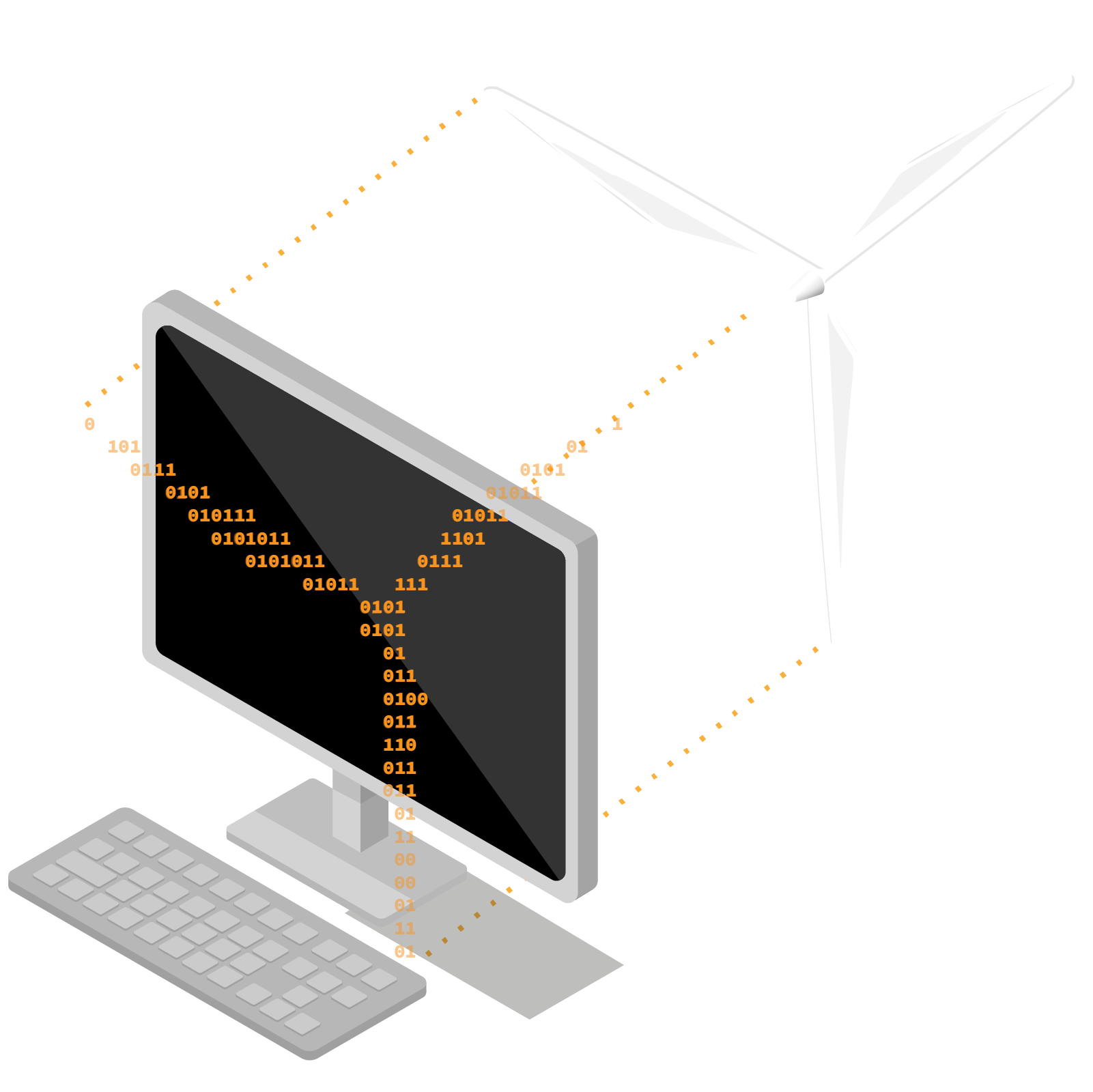
This can significantly affect the wind farm's power output and repair costs. Therefore, the sector is looking for more reliable blades that can cope with the immense forces. Reason for David de Jager to visit Michiel Hagenbeek and Wim Castricum of TNO to dive into the world of rotor blades. Michiel runs blade models in a digital twin; Wim crawls inside actual blades to apply the sensors.
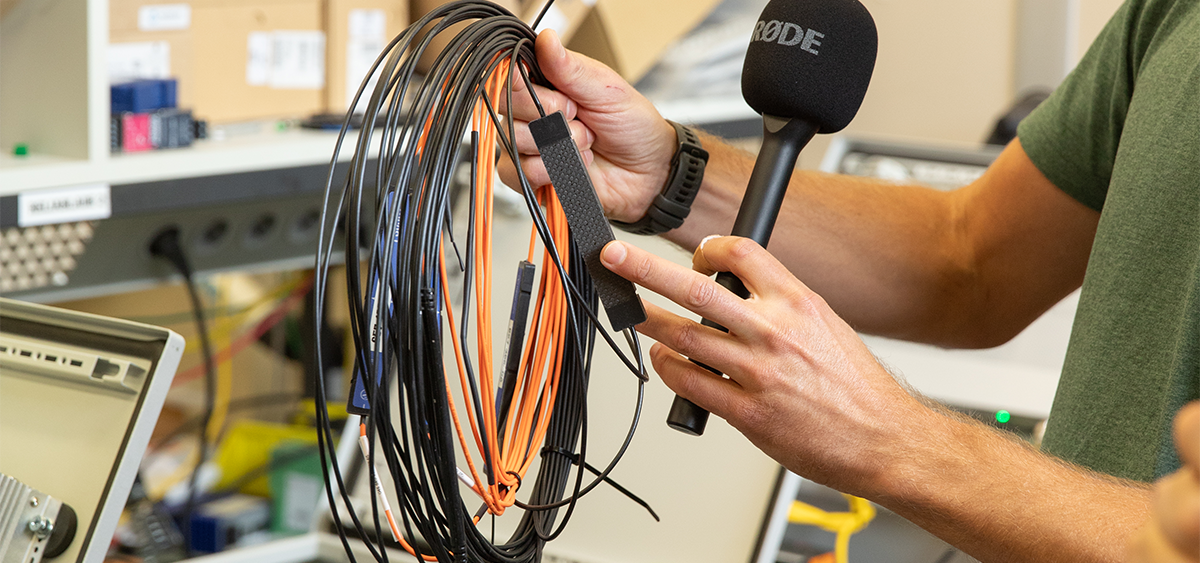
Have a look at Michiel's profile on LinkedIn.
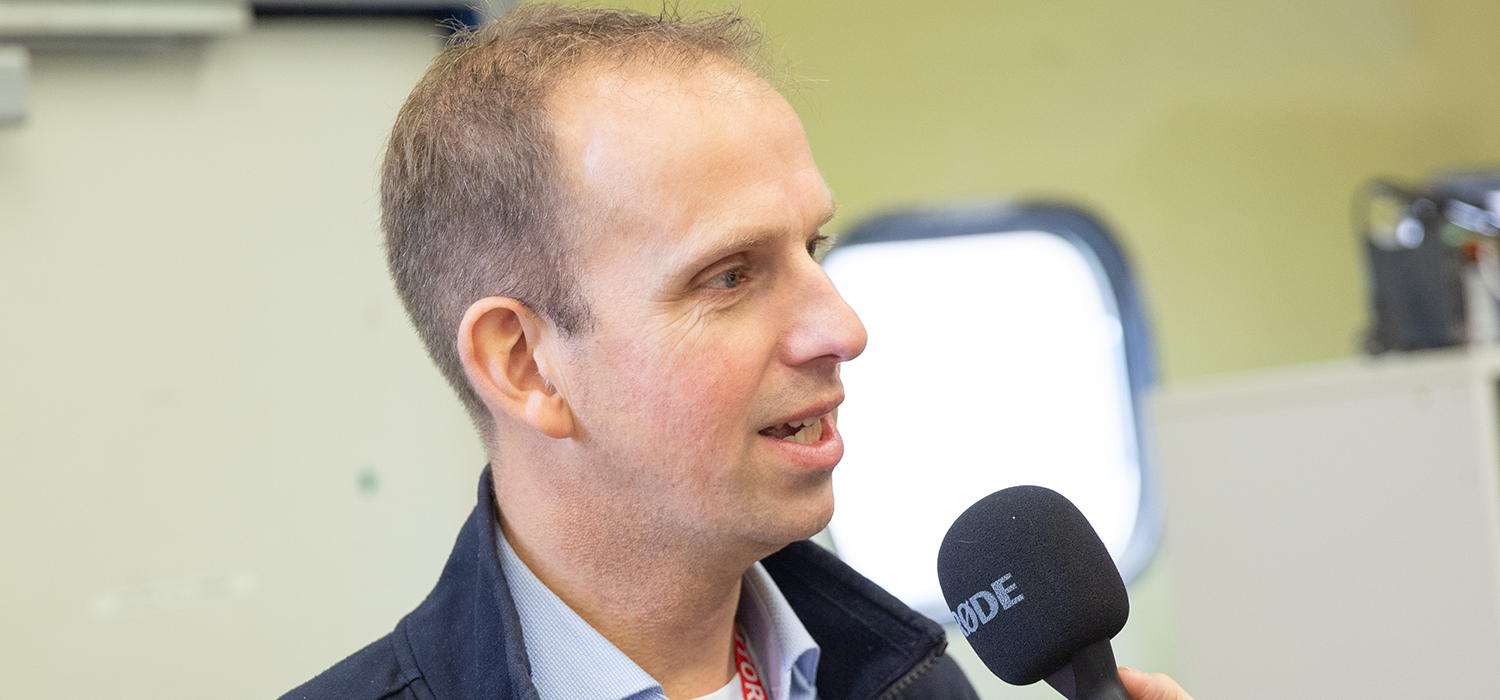
What kind of defects can develop in rotor blades?
Since they have to be in operation for more than 25-30 years, the structure deteriorates, and initial damages can grow over time due to fatigue. Michiel: “We look specifically at delamination of the blades and cracks in the adhesive bond line. For this purpose, we have built a dedicated setup to determine the crack growth of thick adhesive bonds when applying cyclic forces in various directions. We perform an extensive test program to construct a precise damage progression model.”
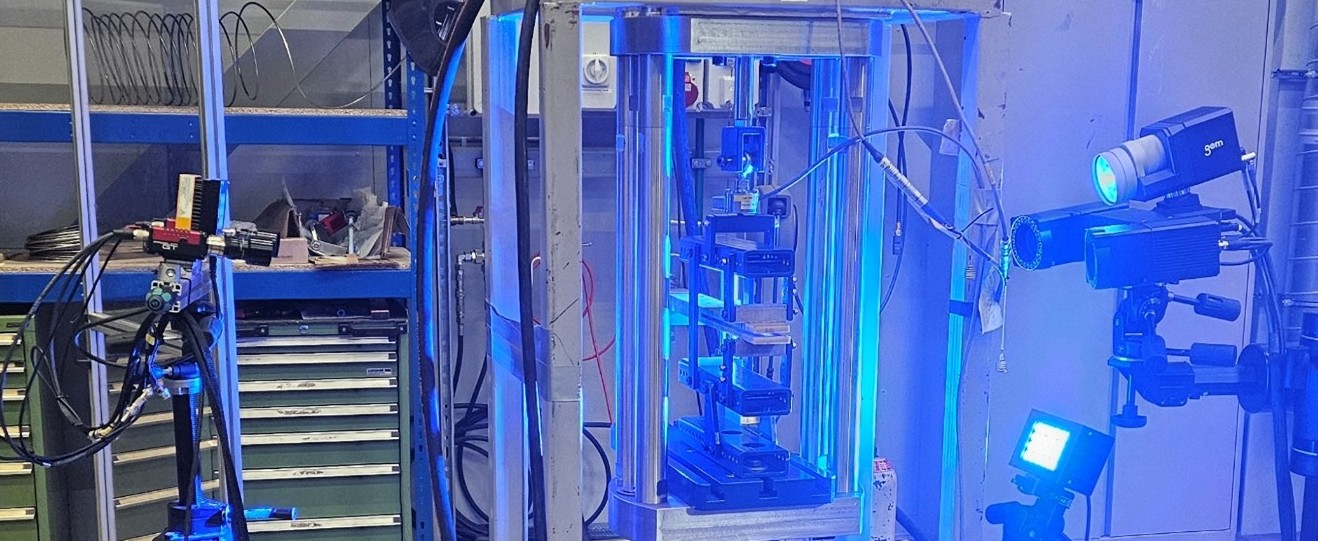
There is no room for a fear of heights or small spaces here!
Have a look at Wim's profile on LinkedIn.

Around 15 sensors will be installed per rotor blade, diverging from sensors to measure the load, twists, shape sensing, and acoustic emissions (sound). The installation takes several days per rotor blade.
Wim will film his activities. We will inform you when we can show you an impression of his activities.
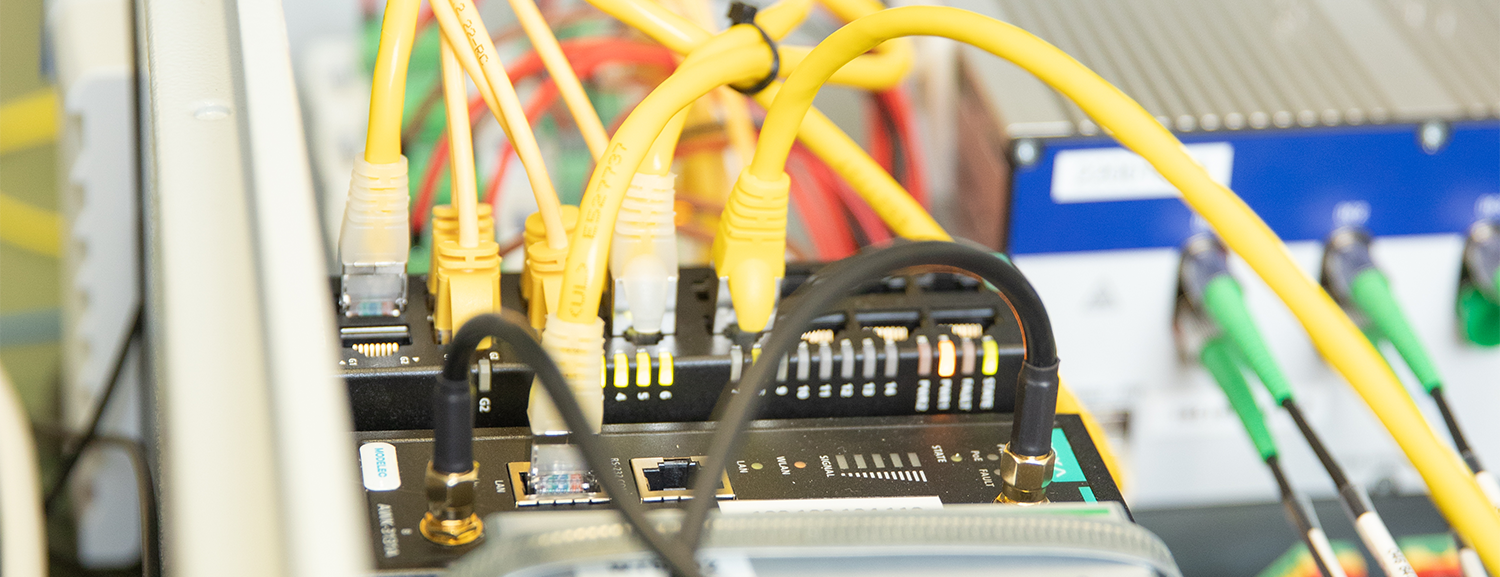
Data data data
Although a lot of data about the rotor blades will be gathered, the rest of the turbine is not forgotten. Wim: “We’ll also measure the wind speed, power output, the pitch of the blade, and more. It’s a new way of collecting this data type but advantageous. We get to trace down the defects at an early stage and get all the information out of this system to create a digital twin as well as possible.”
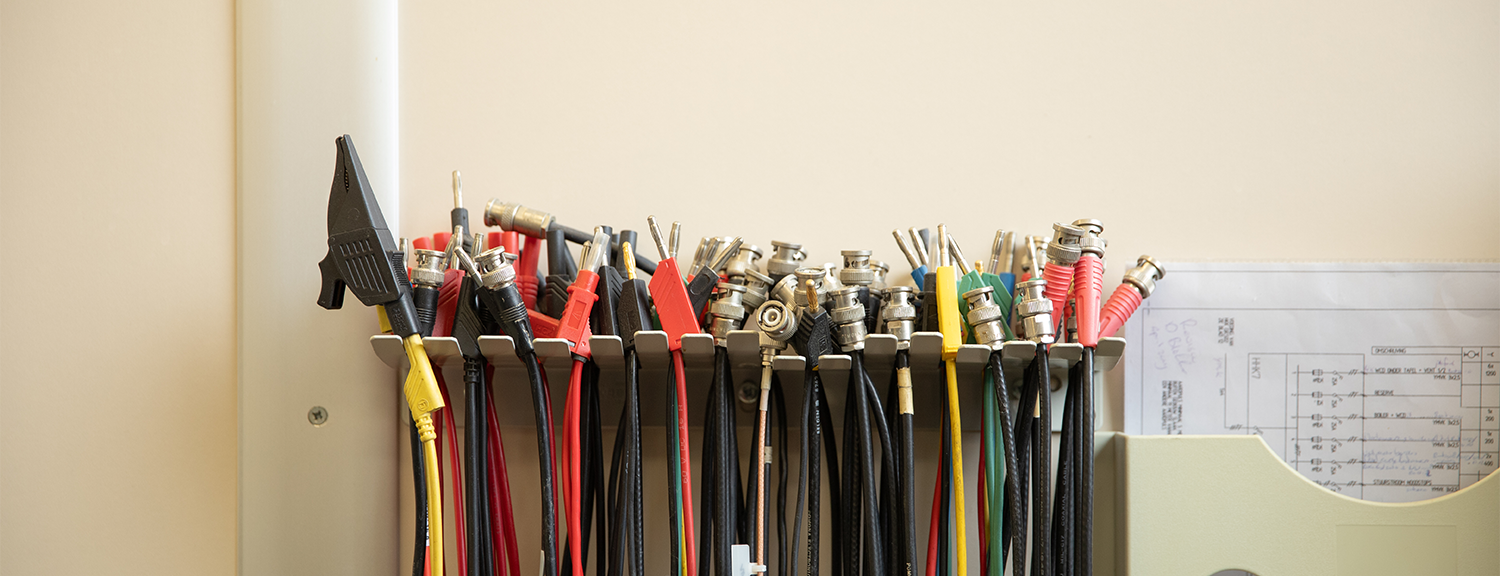
Hear it before you see it
All the data is fed into the digital twin, which can then predict a specific crack or crack growth. The implications of this project are far-reaching. Michiel: “We can use this work in two ways: First, we instrument the turbines that are already offshore, measure the degradation over time, and have this input for our models to predict their condition. The model can predict a defect before you can see it. Based on a signal of the model, the operators will be able to plan the repairs based on the condition, and they do not have to wait for the regularly scheduled interval maintenance.
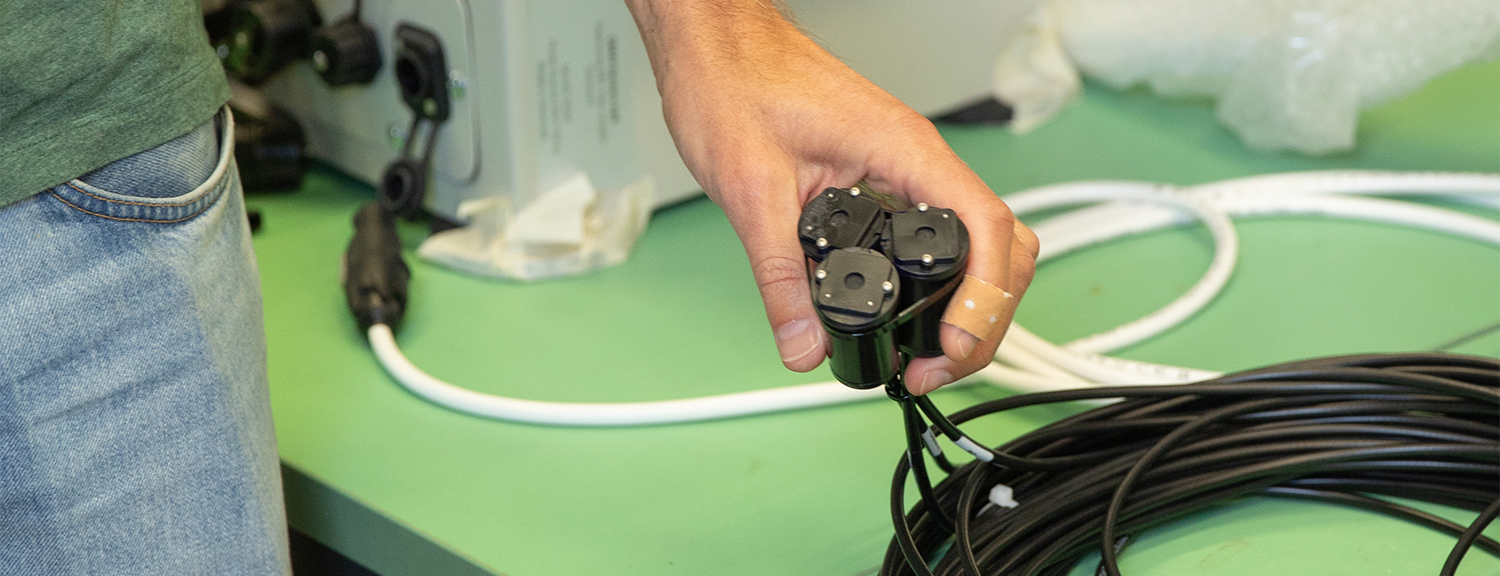
And second, we can use the data to improve the blade design for future wind turbines.” Ultimately, this should help the operator have lower maintenance and repair costs, resulting in a longer operational lifetime for the wind farms.
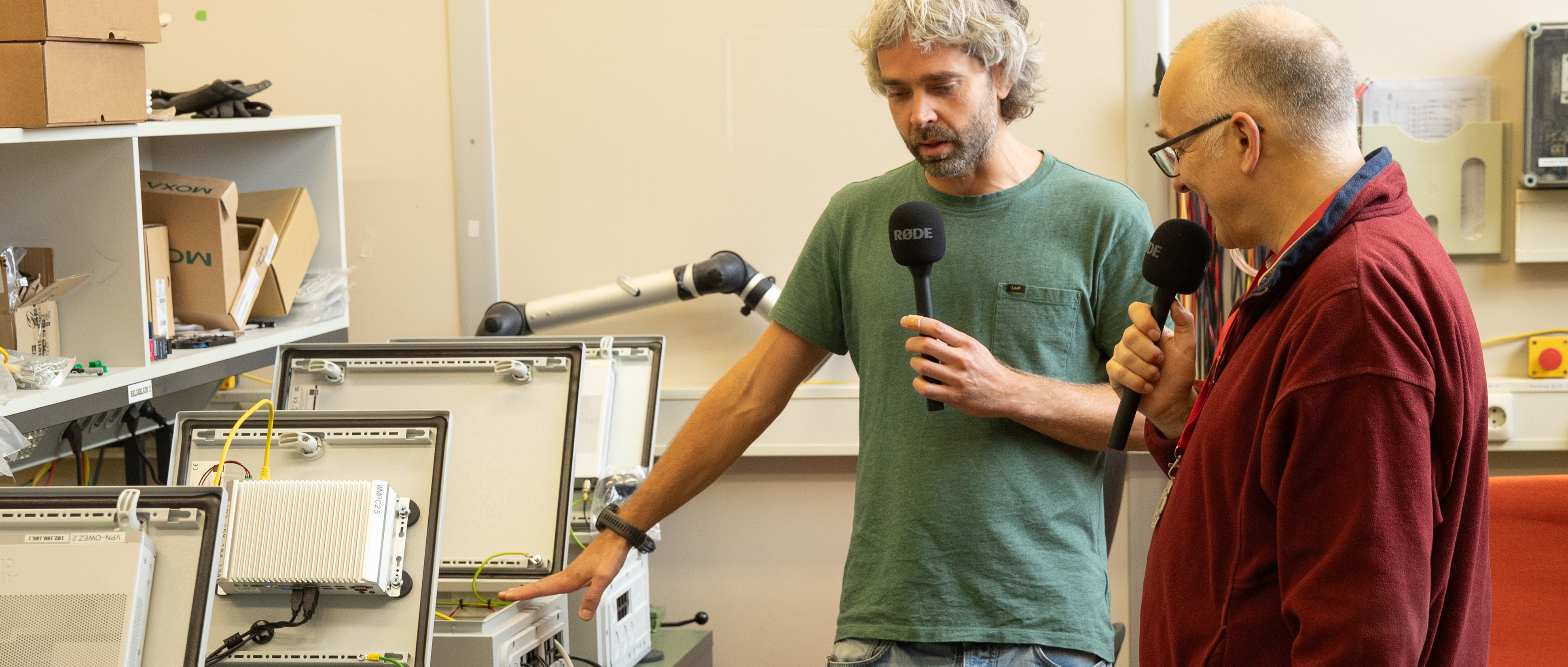
Digital twins of the future
Michiel does not expect each wind turbine to be instrumented this way and to have a digital twin in the future. A few wind turbines in a wind farm may be instrumented, not only in the blades but also in the tower and the foundation. That will be enough to make predictions for the whole wind farm.
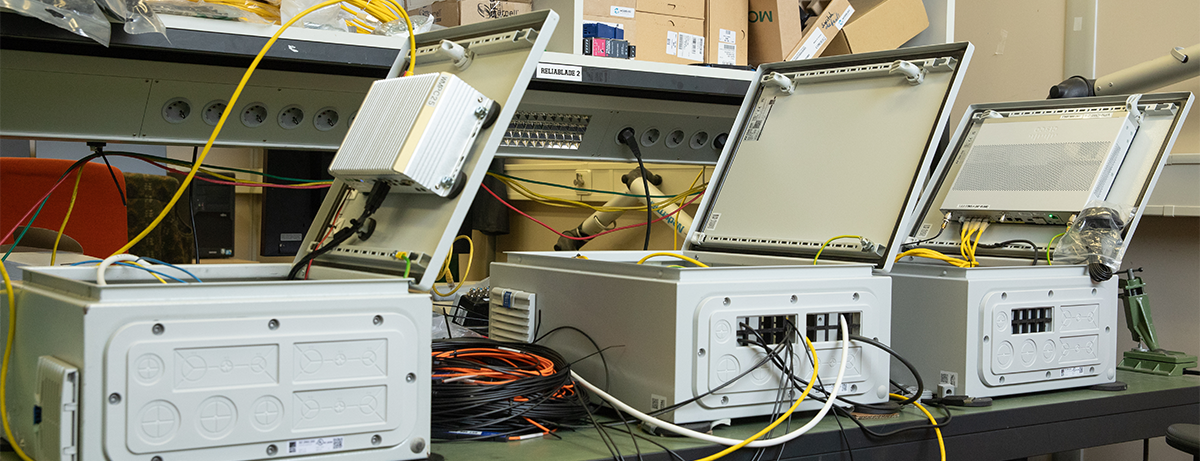
Cooperating instead of racing
Reliablade2-NL follows a Danish-German four-year-long project that we now know as the ReliaBlade 1 project. During this, they had their first digital twin, and they tried to capture the behaviour of the blade. In Michiel’s words: “They did a very nice job, but not all was included yet. So we talked with the partners involved and decided we needed more European cooperation.” Now, there’s this Dutch project, but there are also projects running in Germany, Denmark, Poland, and Great Britain, each focusing on different but related topics. The best part about it? “It’s not a race, it’s a cooperation.” Says the Blade Runner ….
Tarucca: expertise in optical blade sensing networks for structural blade monitoring
TNO: expertise in applied research on digital twinning, structural testing, sensor networks and probabilistic methods.
TU Delft: expertise in structural blade research and data-driven lifetime predictions
Find out more about the Reliablade2-NL project.
© GROW ’25