Install, Load, Repeat
Addressing the effects of lateral cyclic loading on monopiles.
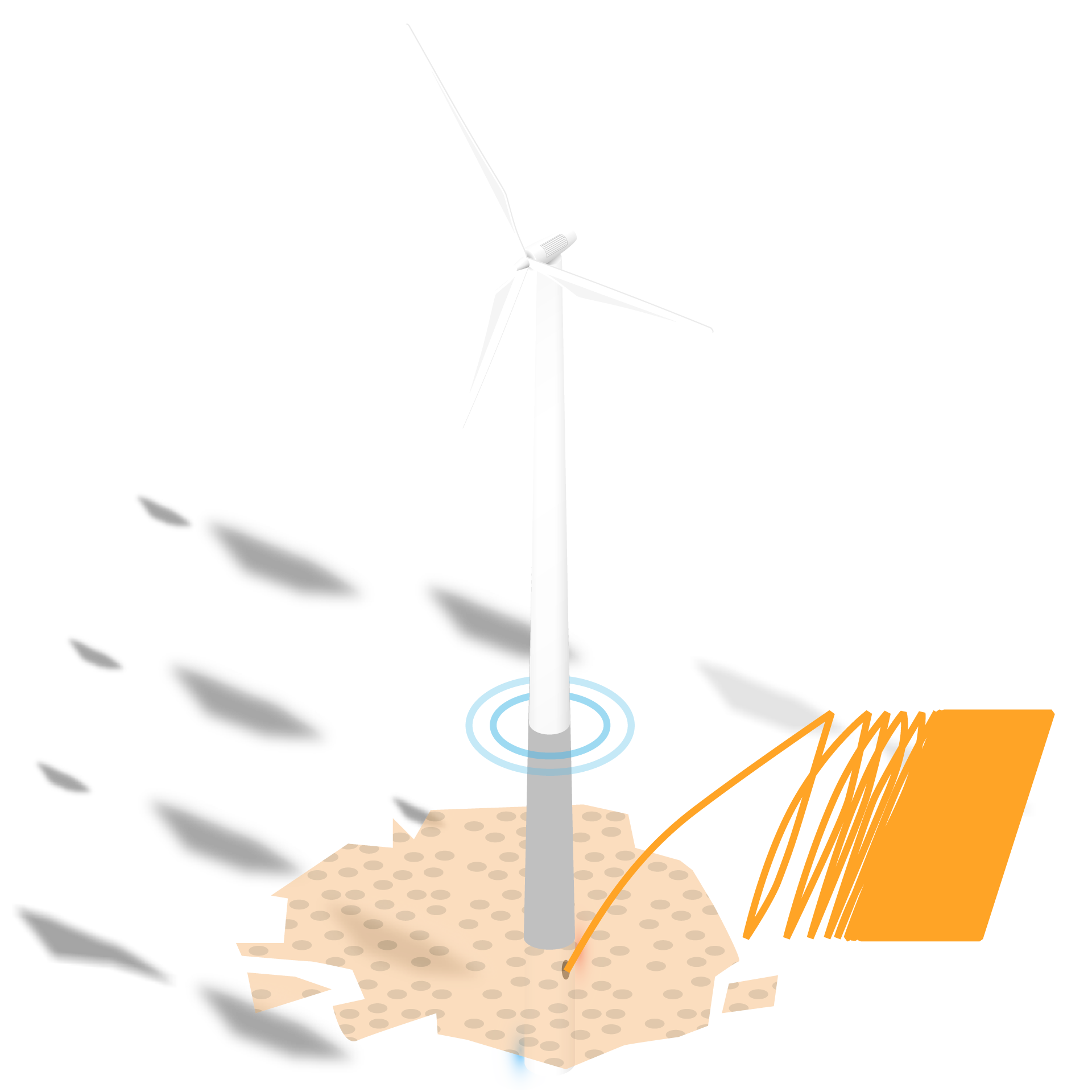
The monopile foundations of wind turbines are subject to repeated (cyclic) loading by wind and waves. These forces are transferred from the foundation to the supporting soil, in a way that may affect the stability of the whole system. As the longer-term impact of cyclic loads is not yet fully understood, monopiles still tend to be designed on the safe side. If we have more insight into this behaviour, we can improve the design of monopiles to obtain lower fabrication costs. Federico Pisanò (Delft University of Technology) and Maria Konstantinou (Deltares) explain how the Monopile Improved Design through Advanced cyclic Soil modelling project (MIDAS) is helping to achieve that.
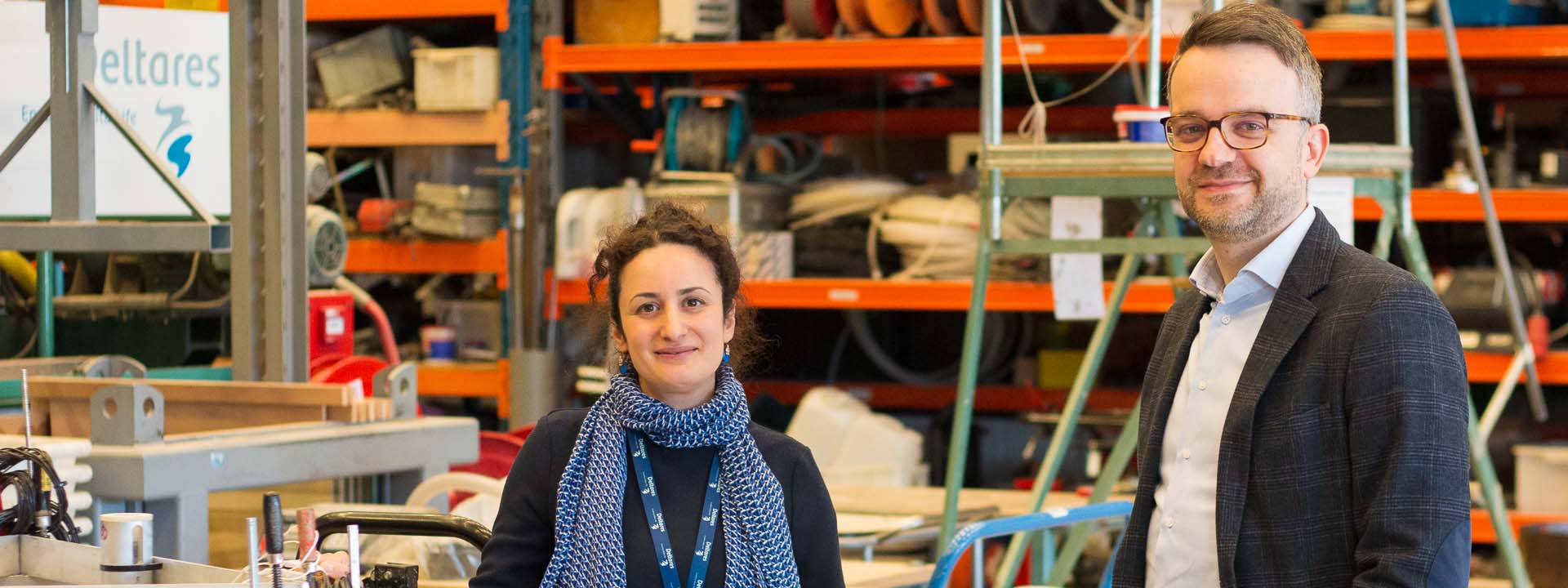
Federico: “If you hit these structures with repetitive loads at the top, this is transmitted to the bottom of the pile in the seabed – and in turn make the pile rotate a little. The pile ‘wiggles’ in the soil. Again and again. This aspect has to be incorporated in the design of the monopiles to ensure that the whole wind turbine structure keeps standing tall even under very high loading cycles, for instance during a storm.”
Have a look at Federico Pisanò's profile on LinkedIn
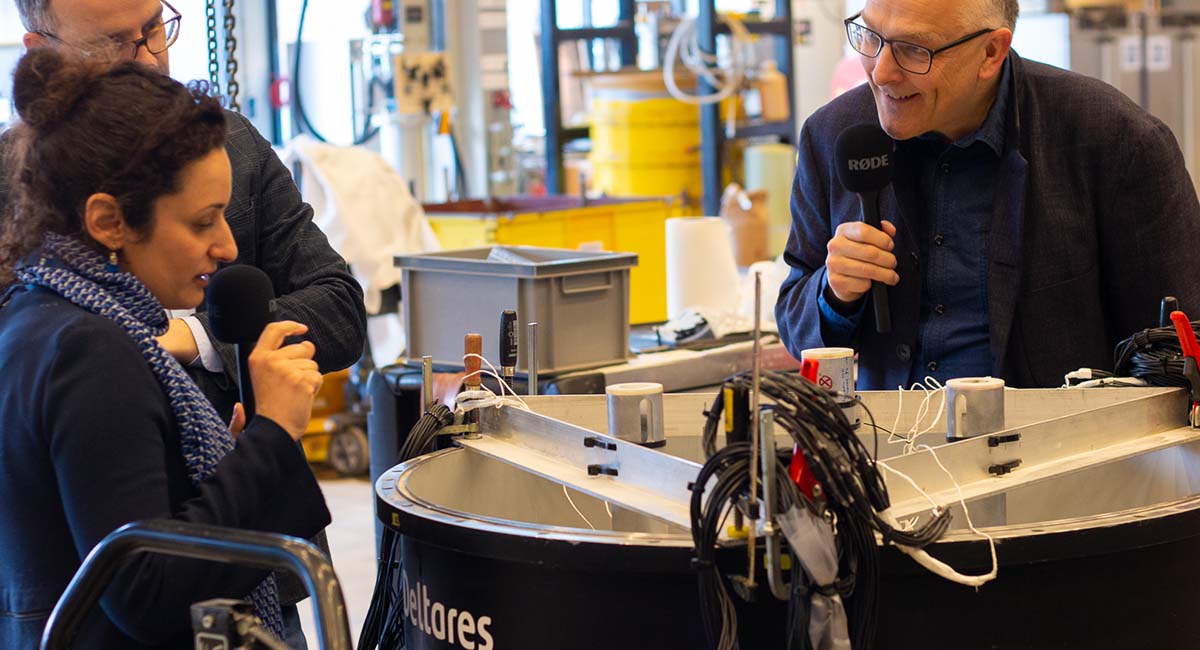
Soil and stiffness
The MIDAS project researches the cyclic interaction of monopiles with the surrounding soil. Both the industry and knowledge institutes realise that there are knowledge gaps regarding how monopiles behave under certain kinds of environmental conditions.
Federico explains: “We want to know how the soil interacts with the pile, deforms cyclically, and how this affects the stability of the structure. For this, we do tests with small-scale monopiles in our laboratories at the TU Delft and Deltares. With this knowledge, we aim to improve our computer models. Which will ultimately help to improve design tools and result in smarter and more cost-efficient designs.” Specifically, it is about understanding how the stiffness of the soil evolves under many loading cycles. The term “stiffness” generally indicates the proportion between applied load and induced deformation. When dealing with piled foundations, this correlation can be represented by using so-called p-y curves, where p stands for the soil reaction that confines the pile in response to the pile deflection (y) under lateral loading.
Have look at this news item on Dutch television with the spinning centrifuge.
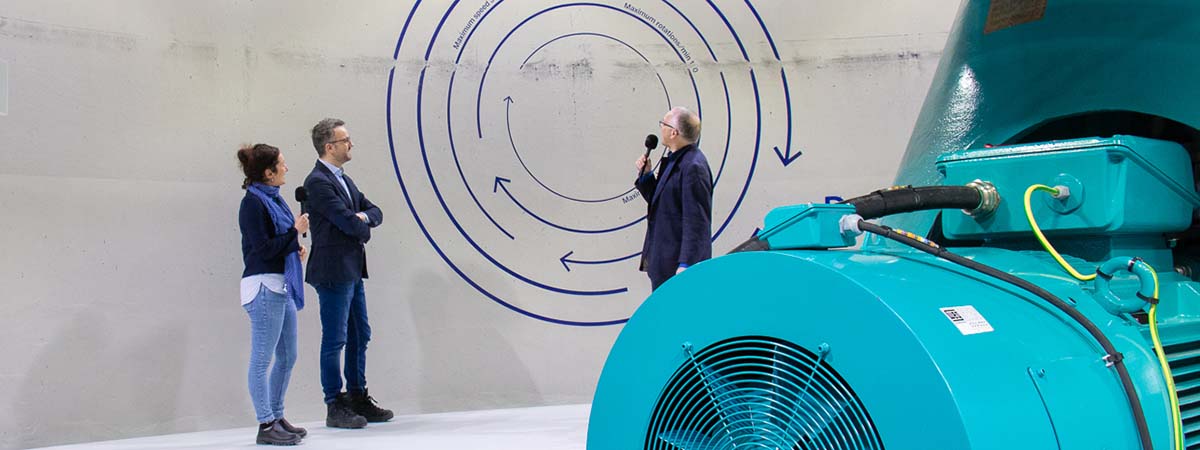
Not peanuts in the end
Have a look at Maria Konstantinou's profile on LinkedIn
Faster than a rollercoaster
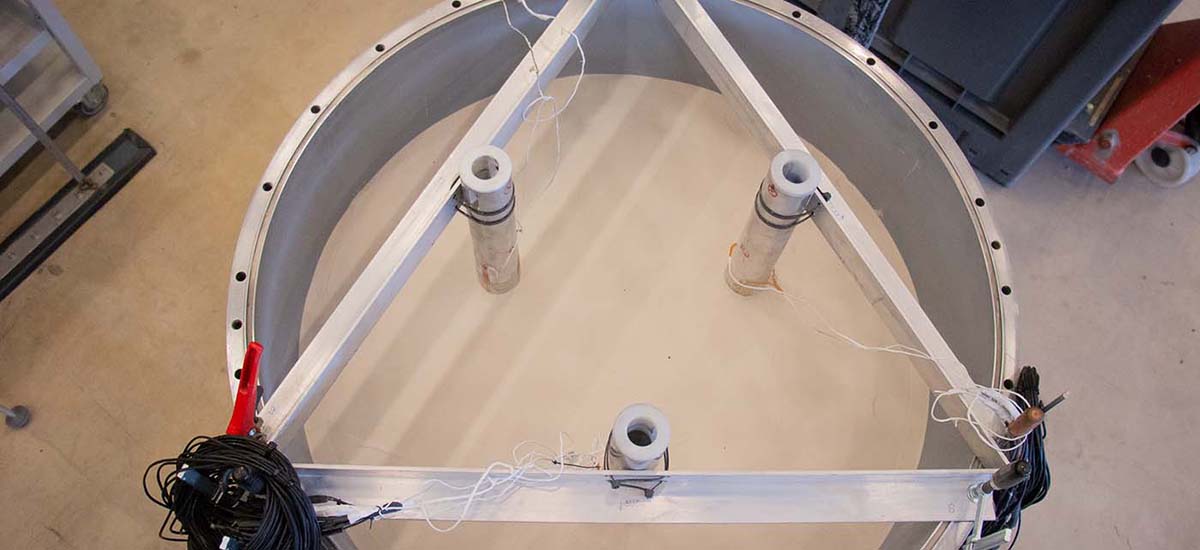
We can subject the model piles to either stress or strain controlled lateral loading in a relatively short time, that would practically not be feasible when using real monopiles.” For MIDAS, the centrifuge at Deltares goes as high as 100 g, hundred times normal gravity. For comparison: on a rollercoaster you will “only” experience 5 g!
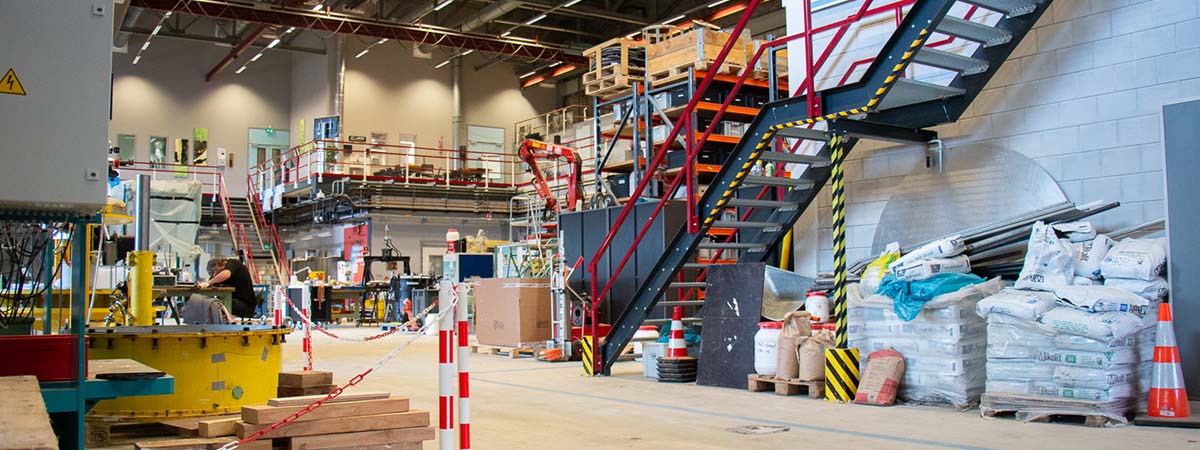
What exactly is it that they do? Maria explains, “we have scaled piles installed in the sand bedding, to which we can apply a horizontal force by means of an actuator. We can control the magnitude and pattern of this force, so as to establish the desired cyclic loading which closely replicates the loading condition of full scaled piles in the North Sea. And while we apply the cyclic loading under controlled conditions, we measure the displacement of the pile head and the axial strains of the pile along its external surface, which enable lateral soil reactions to be obtained after dedicated data processing. For this reason, the test piles are instrumented with several strain gauges along their length.”
MIDAS centrifuge tests are being performed to explore the effect of several governing factors, not only in terms of cyclic load characteristics, but also pile geometry, sand density state and sand saturation conditions (dry and water saturated).
Find out more about the MIDAS project
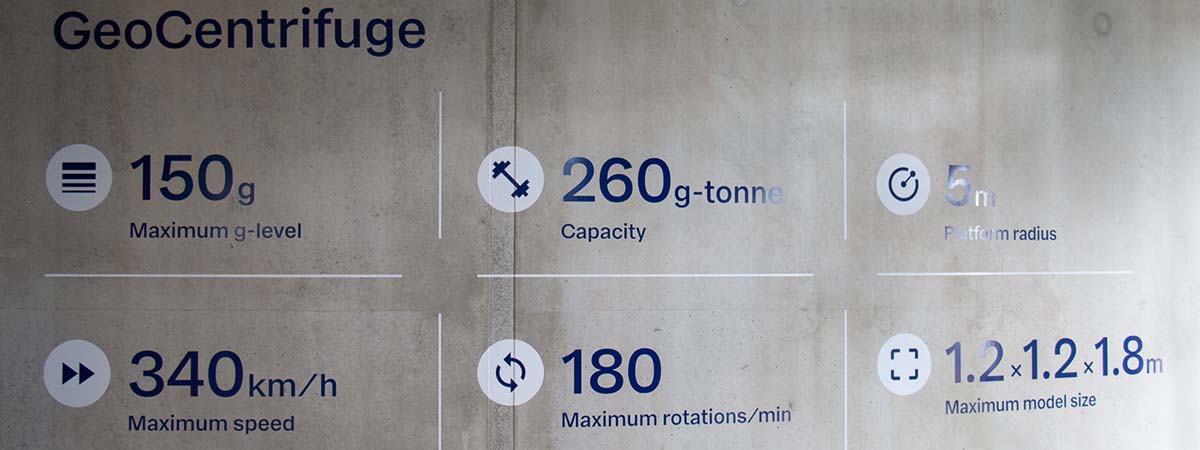
Collaboration is key
In compliance with the overall mission of the GROW consortium, it is believed that the collaboration of research institutes such as TU Delft and Deltares with industrial parties is key for a successful outcome of the project. The industry parties are those that will ultimately apply the acquired new knowledge and insights. In MIDAS these industry partners cover the whole supply chain, from wind farm developers like Shell, RWE, and Eneco, to wind turbine manufacturer Siemens Gamesa, and from offshore contractor Van Oord to equipment supplier IHC / IQIP. “And it's a very good feedback system that allows us, who are designing and conducting the research, to understand how things can be adapted for better use in actual offshore projects,” Federico confirms.
Deltares: expertise on geotechnical research
Eneco: expertise in project development and operating wind farms
IHC-IQIP: manufacturer of foundation and installation equipment
RWE: expertise in project development and operating wind farms
Shell: expertise in project development and operating wind farms
Siemens Gamesa: expertise in wind turbine manufacturing and installation
TU Delft: expertise in geotechnical modelling and project coordination
© GROW ’25