Twist and shake it fast!
Innovations are needed if the offshore wind sector wants to install the huge foundations for the ever-larger wind turbines, as quickly and with as little noise as possible. Well, “The Gentle Driving of Piles (GDP) concept tends to just do that,” Andrei Metrikine confidently states. “This is because GDP uses vibrations, in two directions, with different frequencies, one of those being significantly higher than used in the conventional vibratory driving.”
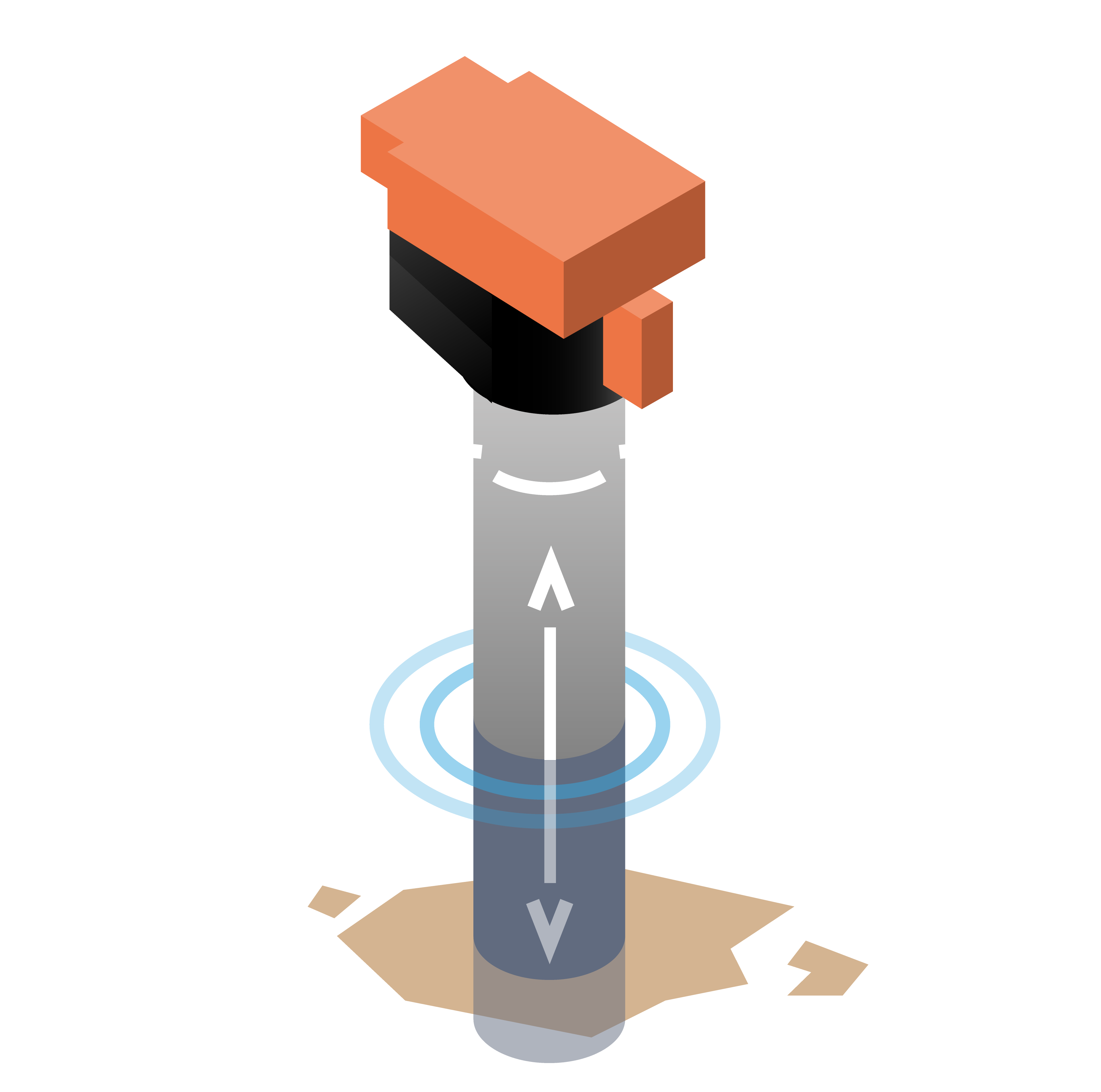
A growing challenge for the offshore wind sector
Currently, monopiles are driven into the sea bed using impact hammering. This driving method generates significant noise levels, both in the air and underwater. The latter can impact marine life. Thus, noise cancellation methods need to be developed and applied to protect sea life, which is very costly. Andrei Metrikine, Antoni van Leeuwenhoek Professor, head of the Offshore Section and Chair of the Department of Engineering Structures at the Delft University of Technology, emphasises. “That’s not the only problem. If the monopiles get bigger, it also becomes significantly more difficult to just ‘hammer’ the monopiles and to mitigate the generated noise.” So, the industry faces a serious challenge, and the GDP concept may be just one of the solutions to address this.
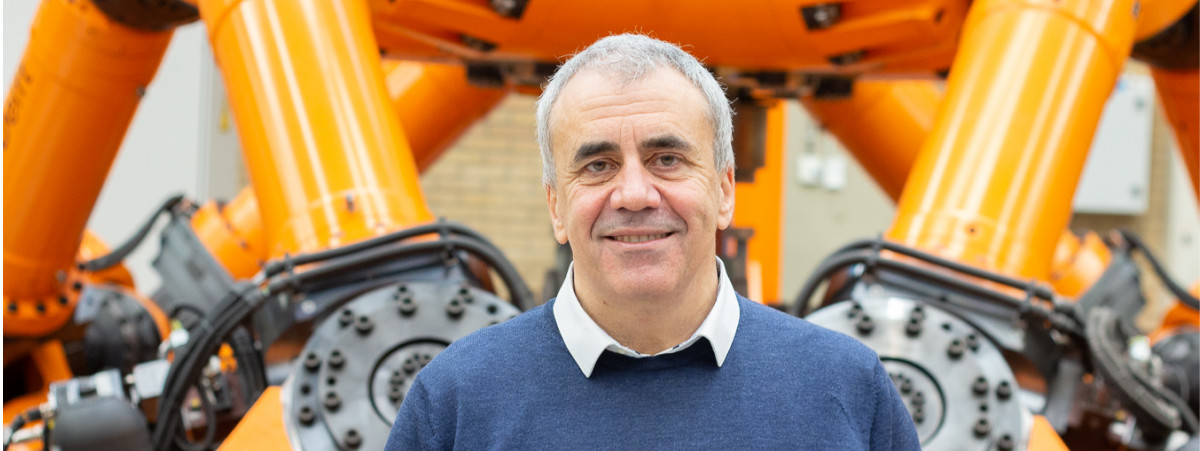
Quickly and with as little noise as possible
This technique can also be used to remove the monopiles in full at the end of their lifetime. “This contributes to a circular design and operation of wind energy,” Andrei explains.
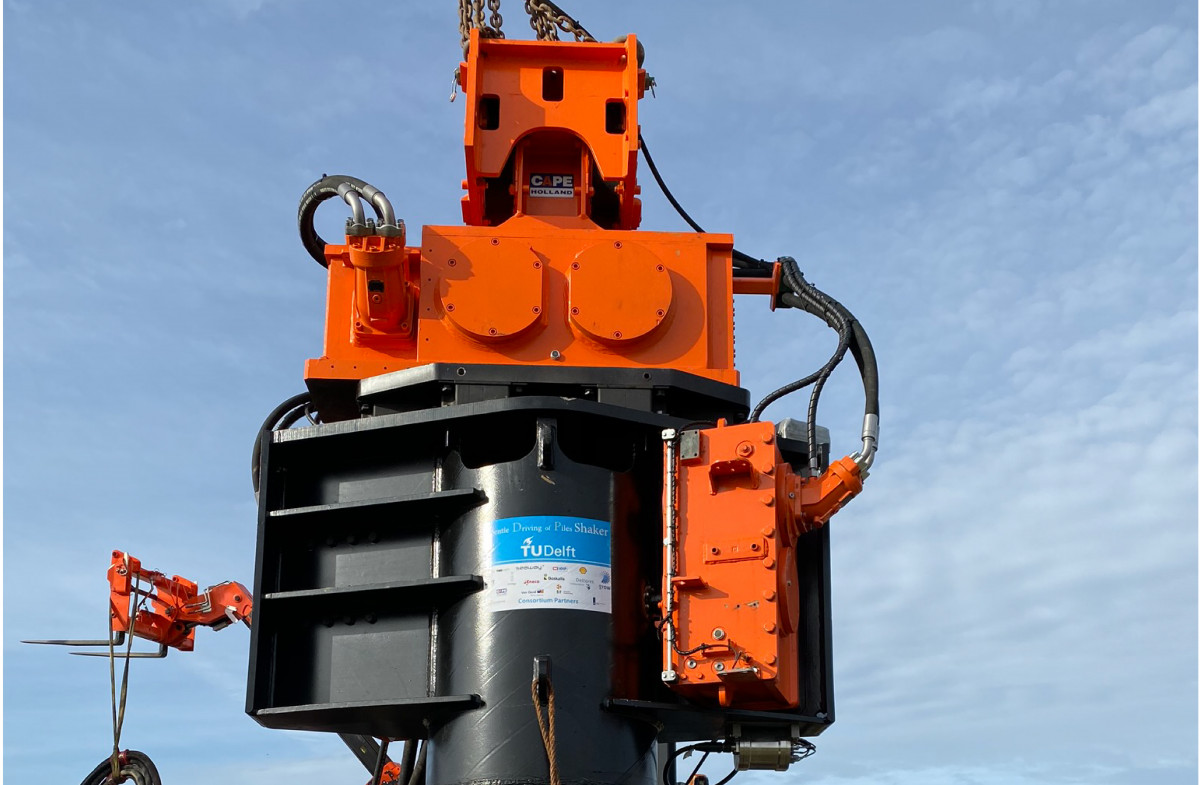
Do current concepts reach their technological barriers?
“Impact pile driving is as old as humans started to build their settlements, and I expect that it will remain one of the predominant techniques in the offshore sector for the foreseeable future.” Engineers will be able to adjust the duration and frequency distribution of the pulse and hence reduce the environmental impact. But the horizontal expansion can not be fully avoided.
Hence, Andrei’s idea is to combine vertical and torsional vibrations. “The gentle driving of piles concept has the advantage that the horizontal expansion, which is the main cause of underwater noise, is significantly reduced as torsional excitation does not cause almost any expansion, while the vertical excitation is minimized. That might be a crucial part of the solution.”
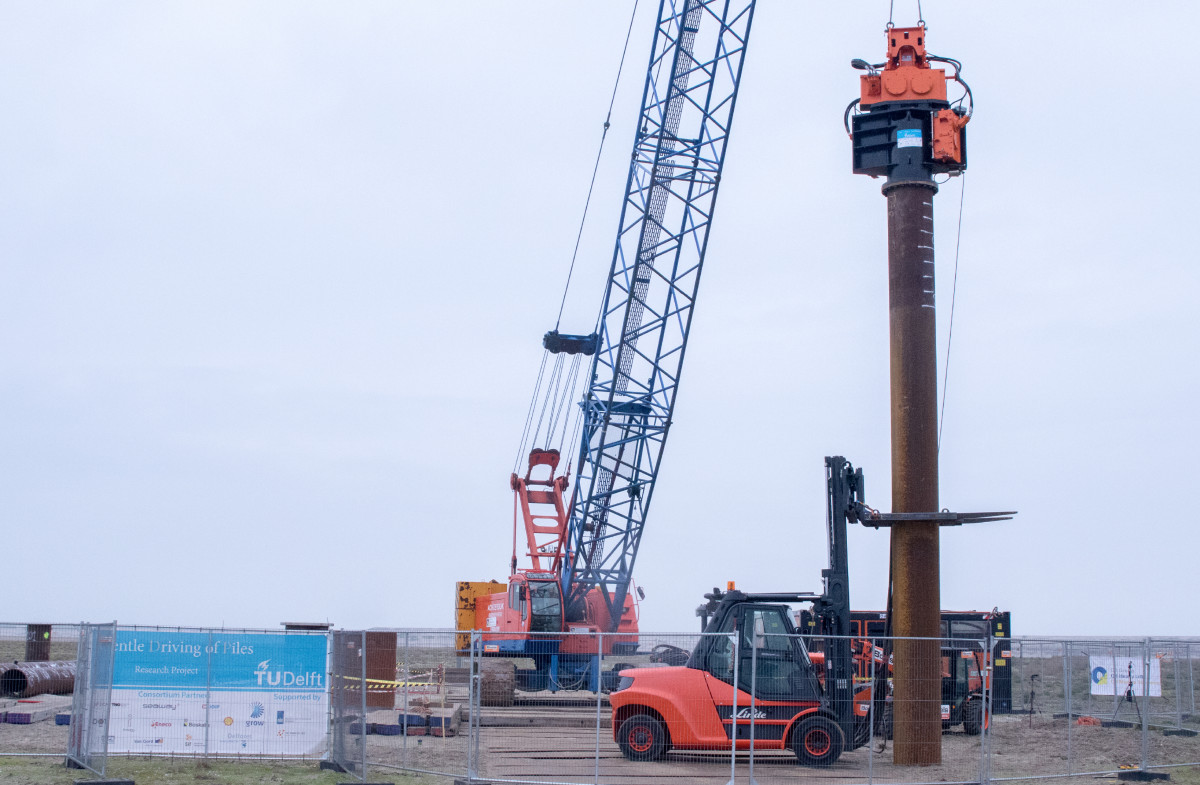
Technology development takes time and good cooperation
“The GDP series of projects started with the idea that the torsional excitation at high frequencies in combination with a mild vertical excitation could just do the job. This was explored in a laboratory test set-up with small piles (see movie underneath) and gave us the confidence to scale up and develop a research program with tests in the laboratory and with larger piles at the Tweede Maasvlakte.”, Andrei continues. “We are fortunate that we received a lot of interest and support from a broad range of industry partners ranging from equipment manufacturers to contractors to project developers. This support is not only financial, it also includes expertise and data from realised offshore projects. By utilizing this expertise, the development can be accelerated.”
The first GDP project has provided valuable insights. For example, regarding the impact of the installation method on the soil bearing capacity, i.e. the capacity of the sea bed to hold the monopile at place during the wind turbine operation. The experiments generated a significant volume of data and insights, which could be used directly by industry partners. According to Andrei, “this data illustrated the viability of GDP and brought attention to things researchers and practitioners had not focused on before”. The project is also used for thorough academic research by several PhD students. This will result in an improvement of the understanding of soil-pile interactions and noise generation, and computer models will be developed and coded that simulate these interactions.
The encouraging results of this first GDP project helped to initiate follow-up projects, such as GDP1.2 SIMOX and GDP 2.0. Andrei: “The main goal of GDP1.2 is to have a complete proof of concept of this novel pile-driving technique before designing and building the full-scale GDP shaker. We will prove that the GDP technique works efficiently in all relevant types of soils, including clay. Furthermore, we will evaluate exactly how we can further reduce the energy consumption associated with the installation of monopiles through decoupling the frequencies and amplitudes of both vibratory excitations. This will also be an automated process that seeks the optimal selection of the driving frequencies and amplitudes”.
In the GDP2.0 project that is currently being set up, a large-scale GDP shaker will be designed, engineered, procured and constructed. The GDP shaker will be tested in a near-shore test campaign, installing and removing a monopile of 4 meters in diameter. And in the meantime, the GDP concept will be further tested in the laboratory and in onshore- and offshore field tests in the so-called SIMOX project, together with other promising innovative installation concepts. The aim is to get one technique closer to certification.
Clearly, the GDP project has had a very good start, but the outstanding characteristics of the GDP technique need to be demonstrated as soon as possible. When asked if this can be done, Andrei’s answer is sweet and simple: “Yes!”
Boskalis: expertise in installation
CAPE Holland: expertise in installation equipment
Deltares: expertise in geotechnical modelling
DOT: expertise in installation
Eneco: expertise in project development
Royal IHC: expertise in installation equipment
RWE: expertise in project development
Seaway 7: expertise in installation
Shell: expertise in project development
Sif: expertise in monopiles
TNO: expertise in noise modelling
TU Delft: expertise in geotechnical modelling and project coordination
Van Oord: expertise in installation
Find out more about the GDP project
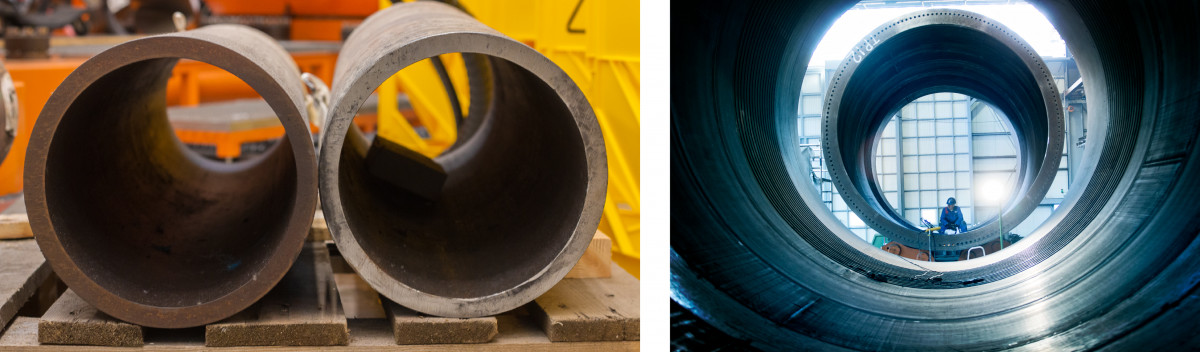
© GROW ’25