Shaken AND Stirred
You’d expect the fabrication of equipment for installing large monopiles for offshore wind turbines to occur in or near a harbour close to the North Sea. But, instead, Hein van Opstal, Charlotte van Verseveld and Rob Sprij, all working at GBM Works, can be found at the firm Kersten in Wanssum, Limburg, next to the Maas River. And not just on any day: they are here to see their jet-ring design become a reality today. First, a jet ring is welded into a monopile section, which will later be part of a 13,4-meter-long monopile. And two of these monopiles will be extensively tested in an onshore test as part of the SIMOX project.
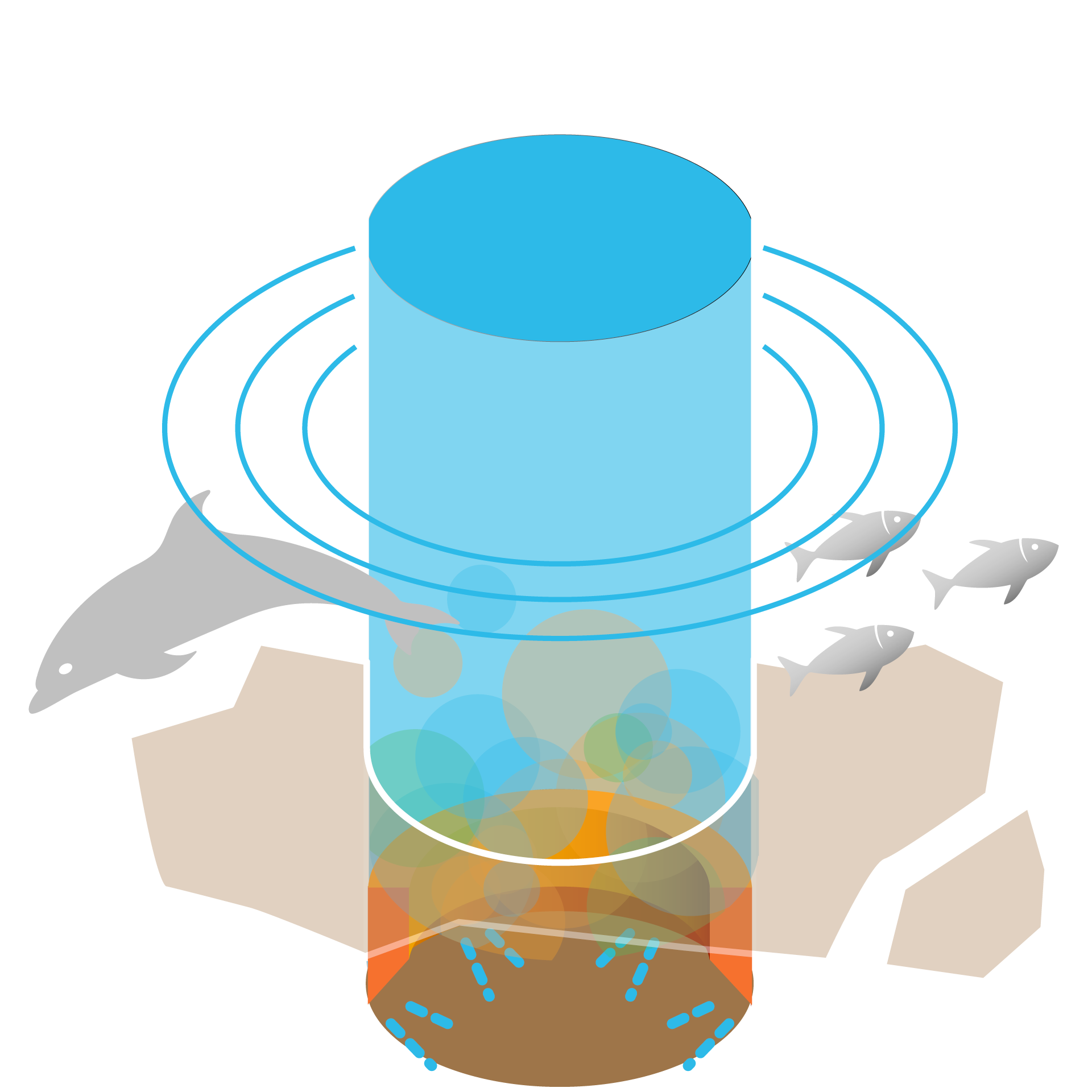
The jet ring is part of the Vibrojet® technology that is being developed in a series of innovation projects that use the acronym SIMPLE: silent installation of monopiles. This advanced technology combines the benefits of two well-established piling techniques - vibratory piling and water jetting - to create a powerful yet eco-friendly solution that can install piles faster, more cost-effective, and with less noise and energy than traditional pile driving methods. In addition, by using high-pressure water jets inside and at the bottom of the pile, the soil can be brought into a state of fluidisation, which reduces the friction in the soil significantly.
Have a look at the website of Kersten
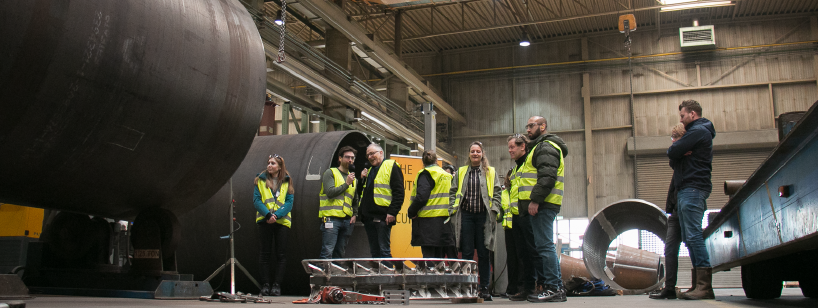
Go to market; how SIMPLE can it be?
Hein explains how the Vibrojet® has been and is being developed in the series of SIMPLE projects: “The main goal of the SIMPLE I project was basically the proof of concept. To determine the basic functionalities of the jet gun in the sand and its added benefit compared to an ordinary vibro-hammer installation. This was done by doing quantitative tests in the lab and 52 qualitative tests in the field.”
Have a look at Hein's profile on LinkedIn
In project SIMPLE II, the objective was to demonstrate that monopiles at a scale of 1:4 (with a diameter of 2 meters and length of 25 meters) can be brought to the desired depth with a retrievable Vibrojet® prototype based on the jet gun in combination with a standard vibro hammer, creating vibrations while jetting clay away and fluidise the soil inside the pile.
Based on the knowledge obtained in the SIMPLE I and SIMPLE II projects, together with additional modelling and the execution of lab tests, prototype(s) are being designed in the GROW project SIMPLE IIB. “They will be tested and analysed in the onshore tests that are part of the SIMOX project later this year, where we will learn more from the pile driving behaviour and resulting soil bearing capacity. And as a next step, in April 2024, in SIMPLE III, we plan to test the full-scale prototype offshore in the SIMPLE III project.”
Like playing with a hose and sand?
The ring has nozzles all around, and each nozzle injects water into the soil. The soil outside of the pile is the most important for the stability of the pile, so fluidising the soil inside the column should have no impact on the stability of the whole structure during its lifetime. Therefore, the ring needs to have the right reach, placement, and workings and must not fluidise the soil outside the pile at the bottom.
Have a look at Charlotte's profile on LinkedIn
As if that isn’t enough to figure out, Hein brings up more tests that the jet ring and water supply must endure. “One is the scour penetration test, so we can see how the ring will survive when it goes through a metre of scour protection. Then, in a second test, we add an impact hammer test. Is the system robust enough? Will it survive? We need to answer these questions before the technology can be applied in the commercial market.
Basically, we are convinced that our technique will replace hammering. However, we need to be sure that if we hit a layer in the ground that is tough to penetrate, we might need to get a hammer to get through. So, that’s why we must be sure that the system can handle that.”
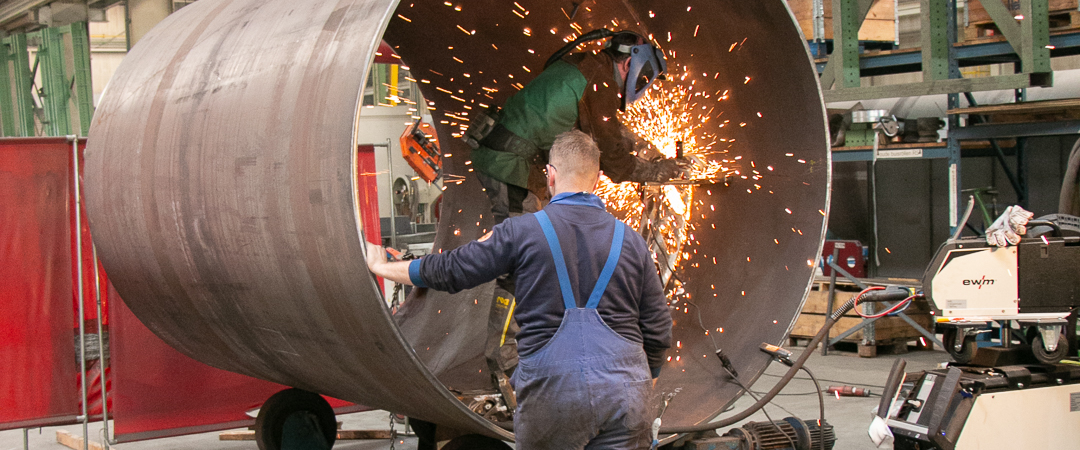
From idea to design, to experiment
Have a look at Rob's profile on LinkedIn
“The advantage of being a GROW partner is the collaboration with other key players in the sector.” Rob explains: “We have some concepts in mind on different components of the Vibrojet. When we visit customers, clients or partners, we can discuss which option best fits their project.”
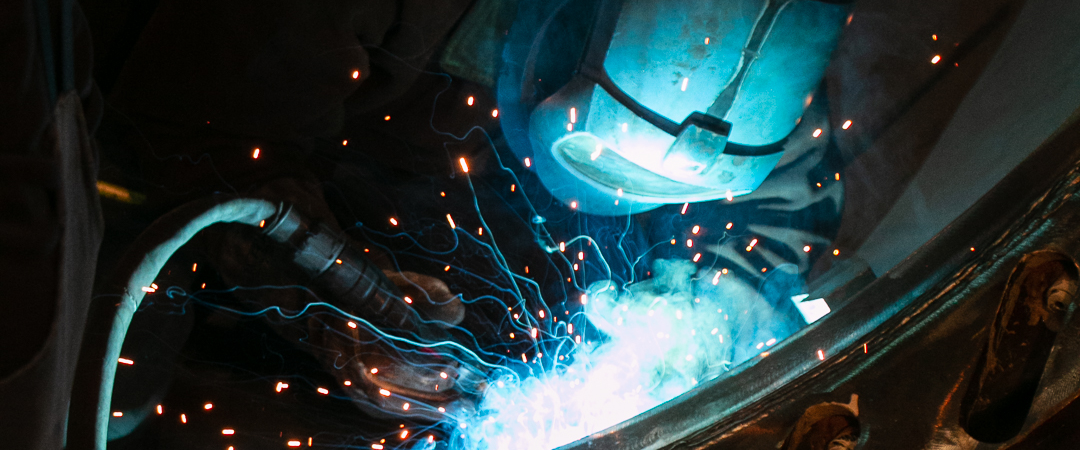
The jet ring will have to be added to the monopile, which means that it will disrupt an existing production chain. “We see that this is a challenge. It has almost kept me up at night. How are the players in the market going to react? How will they cooperate, or how can we make it easier for them?” That’s why sharing designs with partners who can give feedback is even more important. “They have been longer in the process of making more piles, so their feedback is really valuable.”
Cape Holland: expertise in installation equipment
Deltares: expertise in geotechnical research
DEME Offshore: expertise in installation
Thanks to the collaboration within GROW, we came in contact with Kersten, the company that is producing our jet ring now. One of the GROW partners referred him to this company because they are “specialised in the bending and curving metal,” and that was precisely what we were looking for.
As we await the test results, the suspense remains. The pressure is on. And everyone has higher heart rates. Until we can determine that it also works if a full-scale monopile gets shaken and the soil gets stirred.
Eneco: expertise in project development and operating wind farms
GBM Works: expertise in installation equipment
Shell: expertise in project development and operating wind farms
Find out more about Simple IIB
© GROW ’25