The Next Airbender
“Wind turbines love a steady, constant, homogenous wind flow pattern. A wind turbine extracts energy from the wind. The wind pattern it leaves behind, downwind, is rather messy and turbulent. This is called the wake. Suppose a second wind turbine captures the wind in the wake of the first one. In that case, it will generate much less energy: Because the energy content of the wind is already significantly reduced and because the turbulence reduces the turbine’s efficiency to capture this energy.” Says Jan-Willem van Wingerden, full professor at the Technical University of Delft, on Data Driven Control, Wind Turbine and Wind Farm Control. “We’ve developed a way to control the wind flow inside a wind farm and increase the combined energy yield of all turbines.”

Wake steering + Induction control
During the zero’s, Nickelodeon aired the animated series Avatar: The Last Airbender, with Aang as a monk with magical powers able to control natural phenomena like the wind. Jan-Willem van Wingerden is not a monk and is not using magic to bend the air in a wind farm. “In essence, we would like to optimise the energy yield of the full wind farm. This could be achieved by constantly moving the wind turbines outside their upstream colleagues’ wakes, but clearly, this is not an option for the fixed-bottom foundations used in the shallow North Sea. We could also try to control the direction of the wake by misaligning the orientation of the upstream wind turbine with the main wind direction. This can be done by using the yaw system of the turbine. The first turbine will generate less energy, which is compensated by the higher yield of the downstream turbines. This is called wake steering.”
Have a look at Jan-Willem's profile on LinkedIn
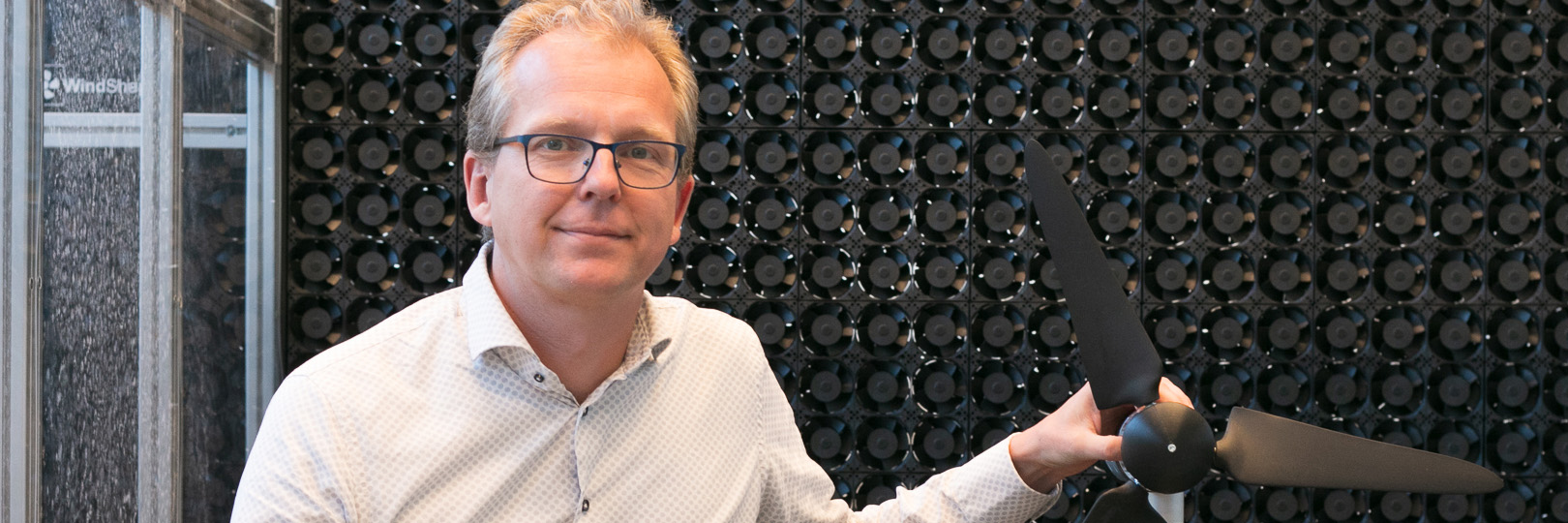
A second option is called induction control. If the first turbine would extract less energy from the wind, the downstream turbine could face more wind. This can be realised by changing the orientation of the individual rotor blades towards the main wind direction, called pitching. If the individual blades capture less energy, more will be available for the downstream turbines.
Bending air to a Helix
But there is more. Jan-Willem: “We’ve discovered that by pitching the rotor blades collectively in a pulsating pattern, we could reduce the wake effect already significantly. But, if we would adjust the pitch of the blades individually in a particular pattern, we could also steer the wake’s position. But if we select the right control variables, we can let the wake disappear after some distance; the wake is fully mixed.” Because of the changing pattern of the wake in time and space, the approach is called the Helix approach.
Data-Driven Control
To find and select the optimal control variables, one ingredient to the Helix recipe must be added: data-driven control techniques, which happens to be the name of the chair Jan-Willem holds at the university. “Most conventional control strategies of wind farms are based on static computational models that maximise the output of a wind farm. But the wind constantly changes, like wind speed and direction, turbulence, the spatial distribution of these parameters, etcetera. So what we do is to feedback the output of a wind turbine to a model that simulates the behaviour of the turbine or whole wind farm, let the model optimise control settings, adjust these settings, let the model learn from the effect of this optimisation step on the output, re-adjust the settings, et cetera. First in the laboratory, then in a real turbine at a test site, and finally in a real offshore wind farm.”
Project Hollandse Kust Noord – Dynamic Wind Farm Flow Control
The Helix approach is further developed in a rather unique multi-annual research project funded by CrossWind, a joint venture of Shell and Eneco, and in cooperation with Siemens Gamesa Renewable Energy and sub-contractors NREL (in the US) and Whiffle. In 2020 CrossWind won the tender for developing a 759 MW wind farm at the Hollandse Kust Noord (HKN) lot. A total of sixty-nine turbines with a nominal power of 11 MW should deliver electricity to the Dutch grid as of 2023. Since the HKN wind farm was tendered under the zero-subsidy scheme, the differentiating criteria for winning the bid was innovations. The Dynamic Wind Farm Flow Control project is one of these innovations.
The Dynamic Wind Farm Flow Control project started in 2021 and will run until the end of 2028. It will develop and implement closed-loop active wake steering (based on yaw control) in combination with the novel Helix active wake mixing technology. The main goal is to mature these technologies and demonstrate these at the offshore wind farm Hollandse Kust Noord. Jan-Willem: “Our techniques can be used to make the wakes shorter or change their direction so that the turbines can generate more energy and the predictability of energy production can be improved.”
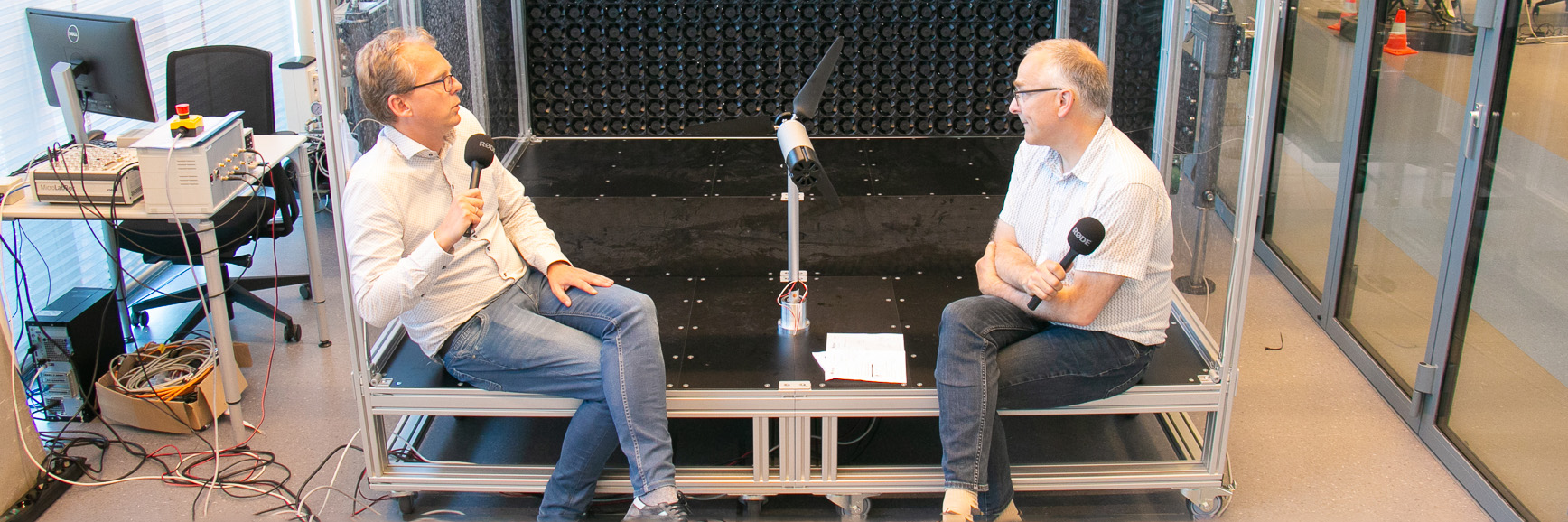
From the lab to the sea
The Helix technology will be explored more profoundly using desktop and computational studies. “We will use high-fidelity computational fluid dynamics studies and detailed loads analysis. These modelling results will be compared with results from wind tunnel experiments. The Helix technology is subsequently tested experimentally at an onshore research wind turbine. When successful, the Helix technology will be implemented at one of the SG 11.0-200 DD wind turbines at the Hollandse Kust Noord wind farm. In parallel, the closed-loop active wake steering technology will be demonstrated at the wind farm.”
The wind tunnel
A new wind tunnel had to be built to achieve all of this. At the TU Delft, Jan-Willem describes that “the tunnel has 700 independent fans, similar to the ones that can be found in a computer, which can be used to create turbulence and time-varying wind profiles. This offers a realistic testing space for the new technologies. There’s also a scaled turbine with a so-called swash plate that helps turn the blades independently but in a similar pattern. This swash plate is a solution that we borrowed from the helicopter industry.”
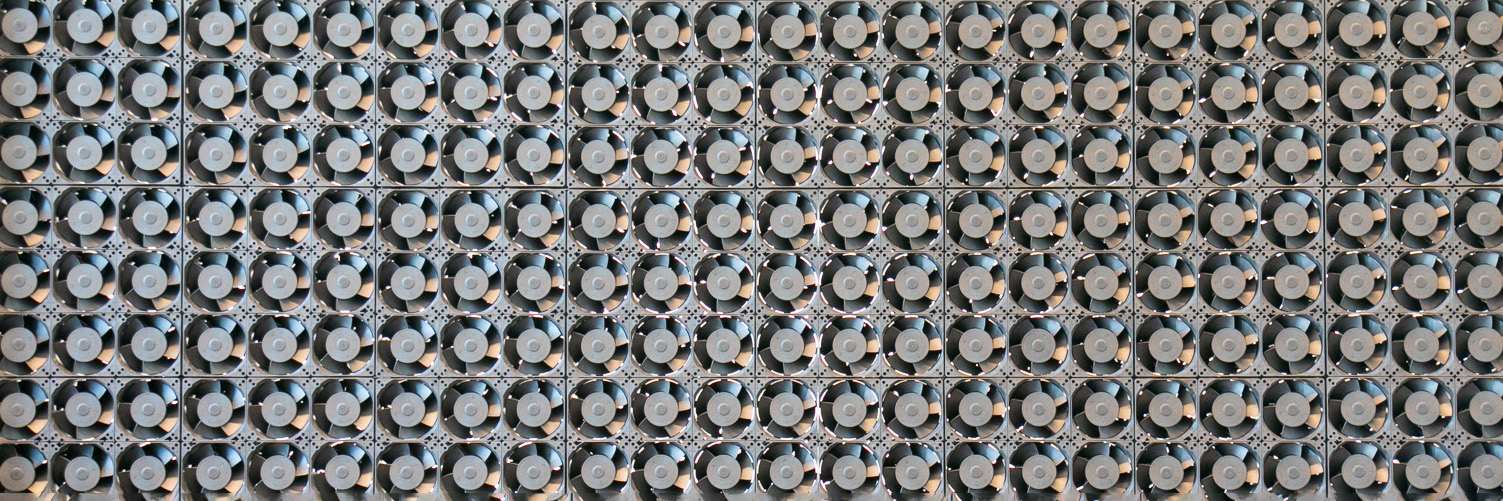
A lucky accident
Taking seven years, the project allows several PhD students, master’s students and postdocs to work on it. They look at all aspects that are important to mature this technology, from the first idea to an application in actual wind turbines at sea. In this case, the idea came from an accidental result while playing with a computer model. The model showed that it was possible to create an optimum in the yield under certain conditions. Jan-Willem: “Playing is important! You need the time and freedom to play, and we are very fortunate that this freedom is also given to us in the current project.”
The future is bright; windy but not turbulent
“We have not seen, and I do not expect to see, any showstoppers,” Jan-Willem confidently states. In fact, there’s little other than exciting prospects. “The energy density of future wind farms - so the energy you could get out of a square kilometre - could be doubled. The main beauty of knowing when and how to do, for example, wake steering, is that turbines can be put closer together. This is what increases the power density.” Jan-Willem breaks the good news: “This is especially exciting for offshore wind farms. Because you either need less space to get the same amount of energy, or you can get more energy out of the same wind farm. And with an expected 2 - 3% increase in the energy yield, the production costs will go further down.” This is indeed mind-blowing.
CrossWind: expertise in project development and operating wind farm Hollandse Kust Noord
Eneco: expertise in project development and operating wind farms
Shell: expertise in project development and operating wind farms
Siemens Gamesa: expertise in wind turbine manufacturing and installation
TU Delft: expertise in geotechnical modelling
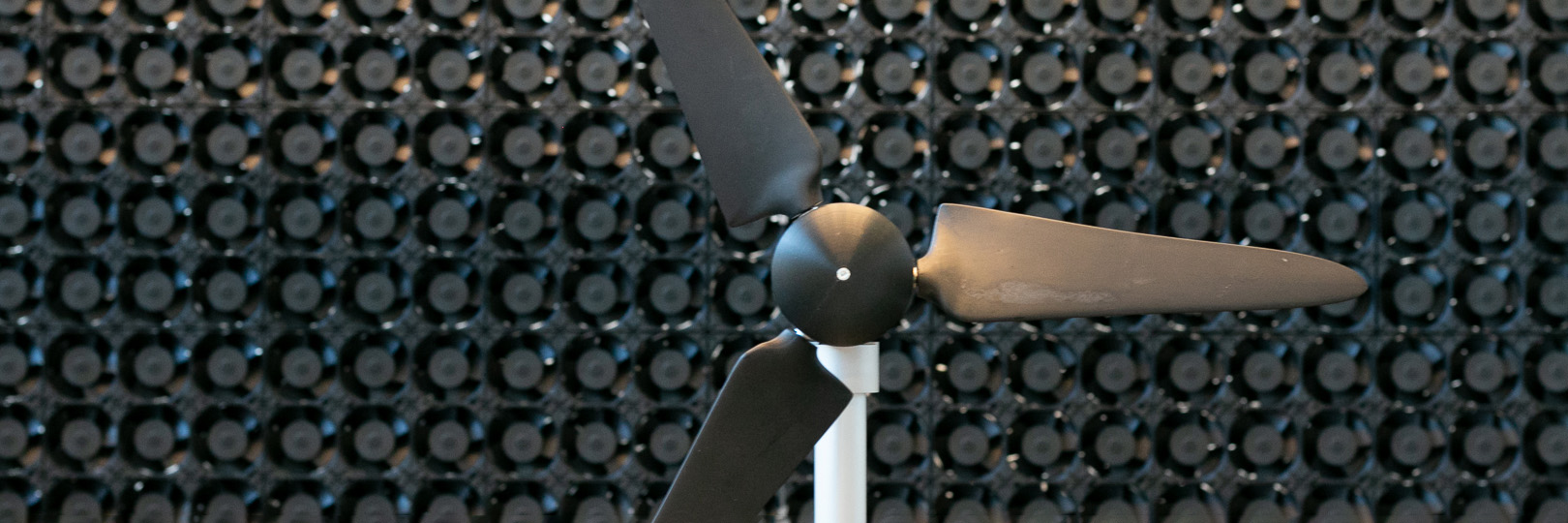
Data-driven airbending
Jan-Willem truly has the cards to become the Next Airbender. Be it less magical or dramatic than the Last Airbender. And possibly also less popular in youth culture. But his quest has the prospect of contributing to an acceleration of the energy transition by improving the performance of offshore and onshore wind farms. In its particular way: that is epic!
Find out more about the Dynamic Wind Farm Flow Control project
© GROW ’25