It’s like connecting steel tubes with duct tape
Offshore wind support structures make a significant part of the total cost of an offshore wind turbine. They continuously need to cope with wind, waves and currents, over the full lifespan of the project. Marko Pavlović, assistant professor at TU Delft, and Maxim Segeren, managing director at Tree Composites, introduce an innovation that might reduce the production cost of such foundations by 25% to 50%.
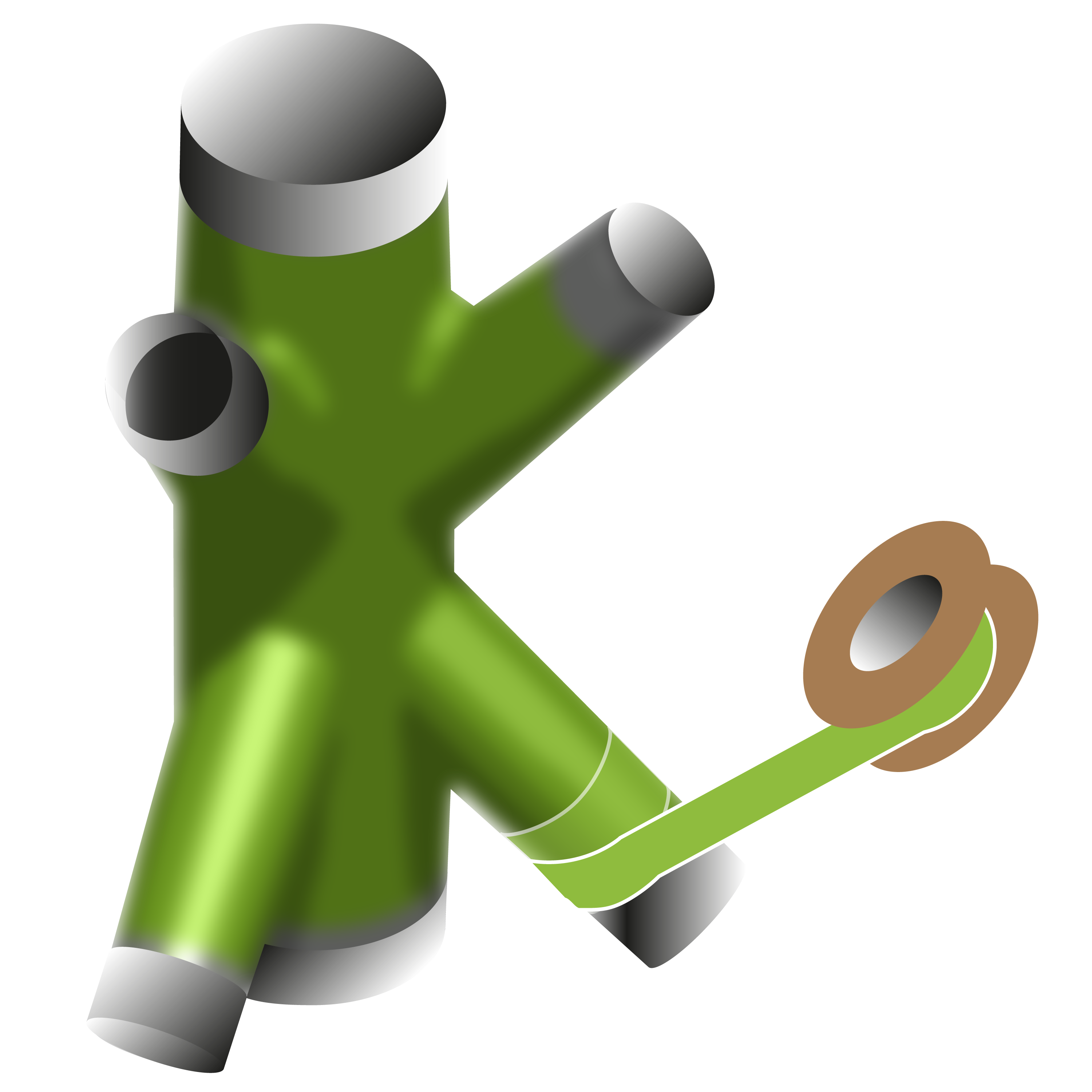
Composites as an alternative to welds
Offshore wind turbines keep growing bigger and bigger and are being installed in deeper and deeper waters. Structures supporting these turbines are therefore constantly subject to increasing loads and a harsh environment. Though jacket structures already have advantageous characteristics, seeing as they’re lighter and require less material than monopiles, they also take more time and money to manufacture. This is why they are mainly used for larger water depths, where monopiles are not a viable option.
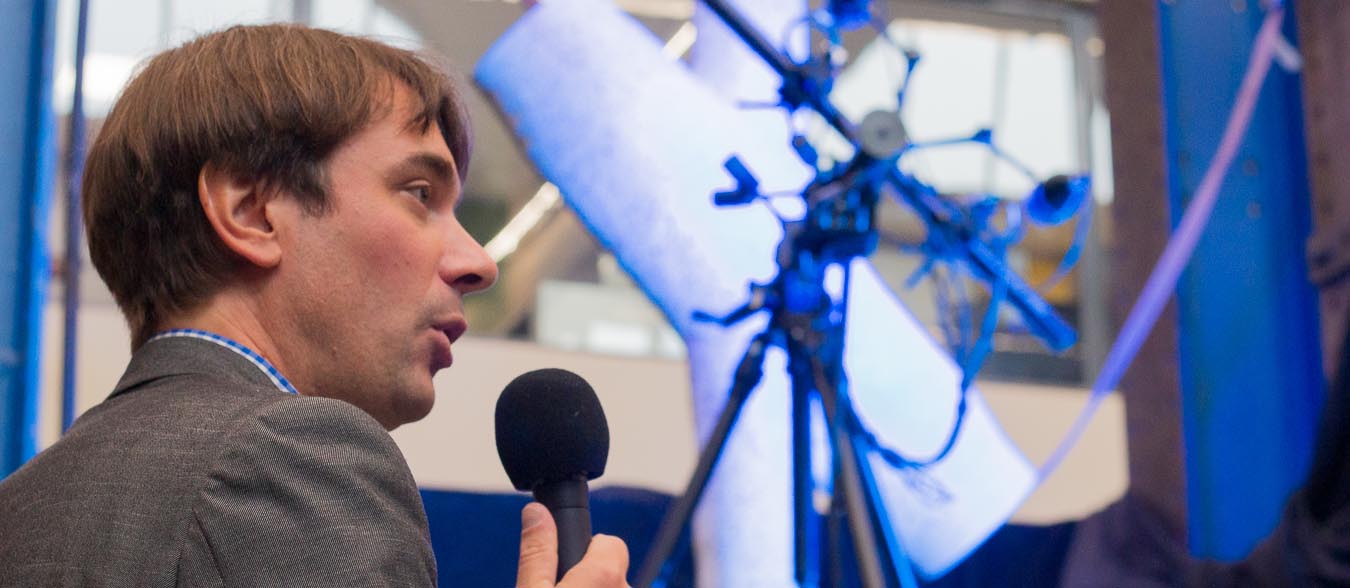
Additionally, they have a complex design, as jackets consist of many joints welded together. Those welds are sensitive, Marko Pavlovic explains: “Jackets have been suboptimal compared to monopiles because they suffer from fatigue loading at the particular details where the tubes are welded together. We try to solve that main detail. We have invented an innovative alternative for the welds, and that is the wrapped composite joint.“
Connecting by using an optimal shape and principles of nature
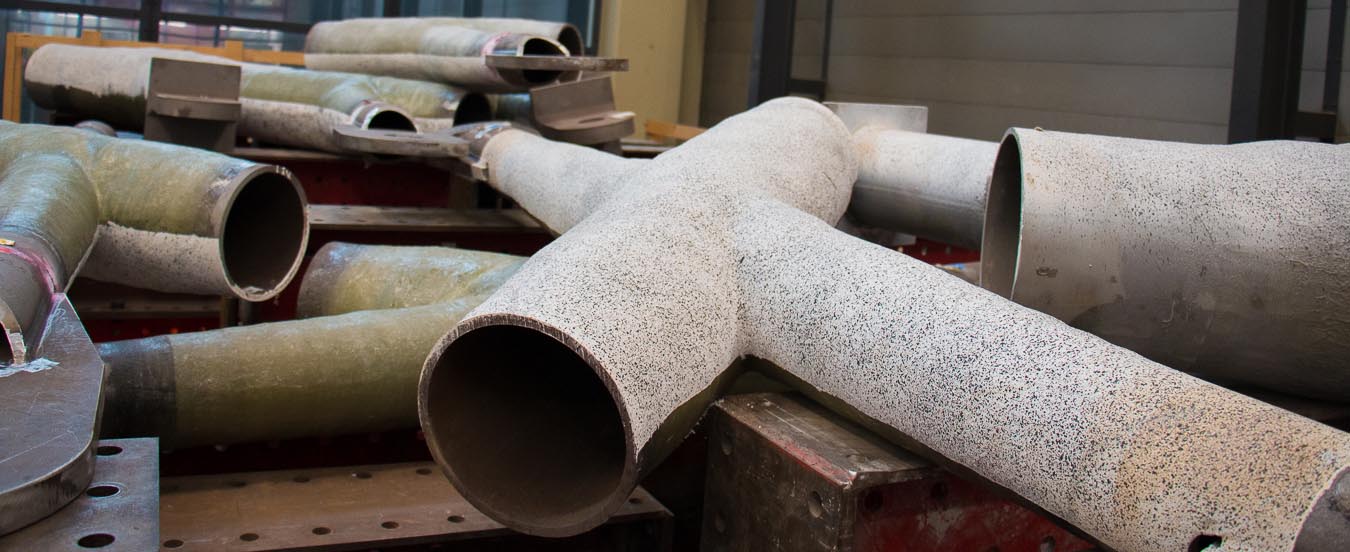
Experimenting, experimenting, experimenting
The current tests are intended to further demonstrate the superior characteristics of the wrapped joint. One of the main theoretical advantages of composites over steel is the large fatigue resistance. The ‘Beast of Delft’ is involved to test this. This ‘Beast’ is a top-notch hexapod testing bench that will be used to put all kinds of different loadings to the wrapped joint specimens. The ‘Beast’, will “pull, twist, turn, and try to break the specimens.” The aim is to actually see the failure of the composite and the bonded interface, such that it provides necessary information for modelling it and predicting its behaviour in the future. When asked if the joints are so far outperforming the conventional welding process, Marko’s answer is short and simple: “Yes.” In fact, the wrapped joint is actually stronger than the steel tubes that are being connected. By increasing the loads to levels that do not even occur in real life, it is one of the tubes that breaks, not the composite joint.
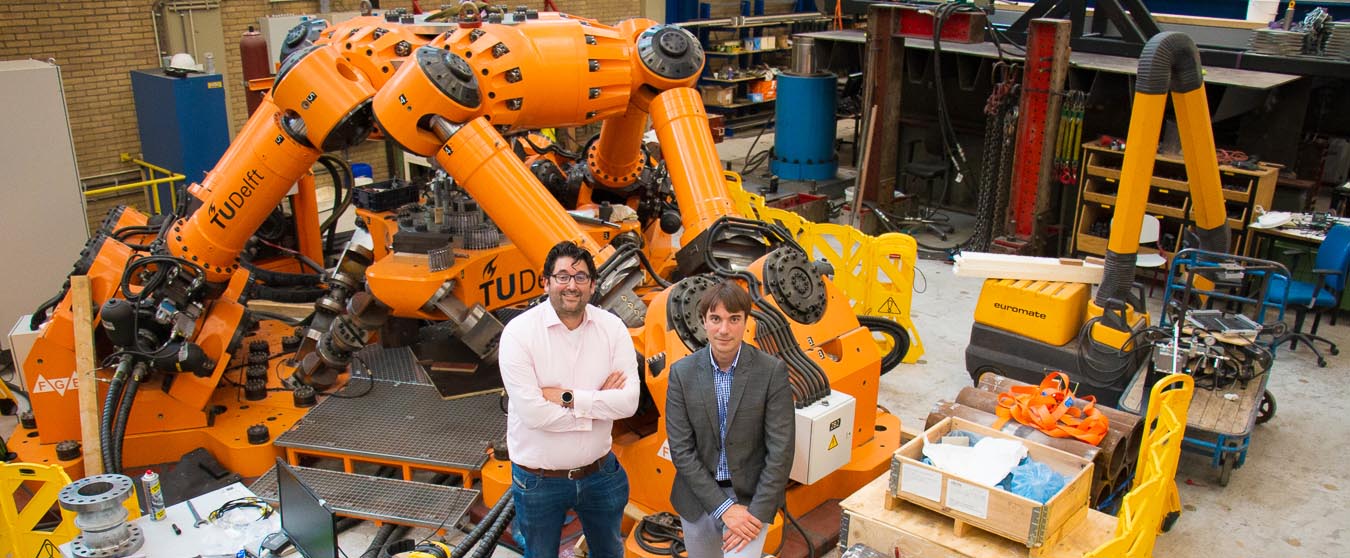
Unique material properties
Another series of tests concentrate on the optimisation of the material that is used. This includes making and cutting composites into shapes that can be torn apart “as if you tore apart paper,” Marko describes. Marko confirms that these particular tests that help to understand the material behaviour are not new. “It’s a well-known standard experiment to test the fracturing of a composite material. But the material itself that we are using is new.” Steel, the material that has been used so far, has a couple of set material properties that can hardly be changed. Composites are in that respect entirely different, as Marko explains: “When you’re making a composite, you’re actually making it yourself. It’s a tailorable material, so its material properties can vary depending on what fibres or which resin you use. So for each new composition of the material, you have to do a series of tests to learn about its properties.”
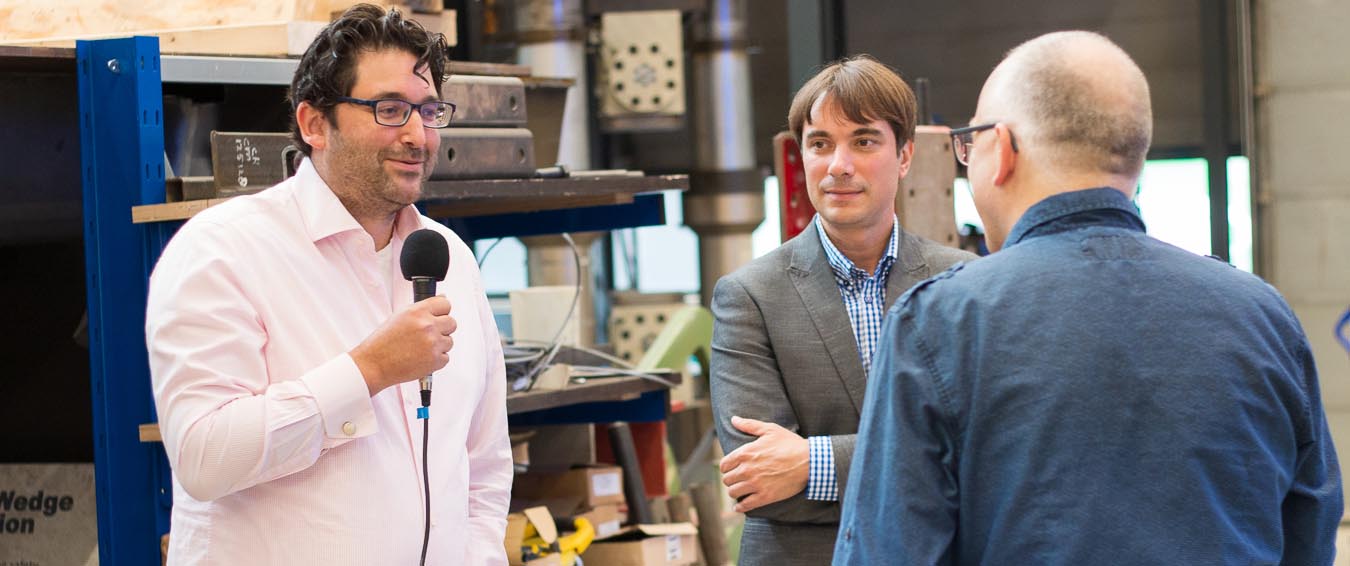
Sharing expertise and essential collaborations
Unsurprisingly, this is another great collaborative project with a diversity of partners involved. Maxim Segeren of Tree Composites lists numerous associates that contribute to the project’s success. “We’re currently in the phase of designing the full jacket in such a way that we can design the joints together with Enersea. And Siemens Gamesa provides the data on turbine loads that reflect real-life situations.” And HSM Offshore, who also builds jacket structures for offshore gas, and Smulders, responsible for the mass production of jackets in Europe, share their expertise to bring the research to an even more impressive level.
The future, a new standard
Additionally, Maxim aims to commercialize the composite joints: “We believe that the composite joint will become the new standard of connecting multi-membered joints. So, instead of welding, which has all these negative effects, we would like to provide the full joint as a building block in jackets. Why? Because we can significantly reduce the amount of material that you’d need to produce renewable power and we can contribute to the required acceleration of deployment of offshore wind by reducing lead times of jacket structures.” And since lowering material needs, means lowering the costs, this innovation is clearly another revolutionary step towards affordable renewable energy.
AOC: Providing expert input on materials
Büfa: Providing expert input on materials
Enersea: Design of the jackets foundations
HSM Offshore: Review and guidance from a constructor point of view.
Salzgitter Mannesmann Renewables: Expert input and review on steel and welding.
Shell: Expert reviews on the jackets designs and financial contribution
Siemens Gamesa: Providing turbine loads for the jacket designs and reviewing.
Smulders: Review and guidance from a constructor point of view.
Tree Composites: Development of design and manufacturing of composite joints
TU Delft: Leading the consortium and knowledge development on behaviour of the composite joints
Find out more about the WrapNode-I project.
© GROW ’25